EMI Shielding for Automotive Applications
The boom of technology-enhanced the automotive industry just as it did the rest of our lives, but with the capacities that technology enables – in-car Bluetooth, GPS, WiFi, and more – came a greater need for EMI shielding. In the automotive industry, with safety being the absolute priority, it became more important than ever that the highest quality EMI shielding gaskets were used where they were needed. A car is only worth as much as it can sell for, but safety is priceless. A huge part in determining the utmost reliable EMI shielding solution is its part compatibility – all the parts must work cohesively for the vehicle to function.
Engineers face challenges with more complex applications, as total compatibility between parts becomes more difficult to achieve. Similarly, the complexities pertaining to EMI shielding for automotive applications hike up the total cost of supplies and materials. A shielding component that is reliable and highly-compatible must be able to withstand not only the speed and agility of a modern-day vehicle but the forces of nature that it might encounter, too. For this reason, EMI shielding component manufacturers who specialize in complex automotive applications are being sought out for their refined expertise.
Reliability Among Automotive Components & EMI Shielding
Of course, just any EMI shielding part will not suffice for automotive applications. The shielding component materials – like the rest of the automobile’s parts – must be able to withstand adverse environmental conditions. Your EMI shielding component should be able to function properly in adverse temperatures, humidities, velocities, and more. They should also be capable of withstanding shock, vibration, and other unexpected turbulence.
When it comes to temperature, standard electronic components can operate between -40ºC and 125ºC, meaning that any reliable materials should be able to function properly on both extremes of that spectrum. When measuring for shock resistance, ensure that occasional, high impact-related shock does not reach above 20 g’s and general vibrations don’t span past 3 g’s. If the vehicle operates in extreme environments that cause it to surpass the limitations of these criteria, mounting your component to the vehicle’s engine block has been found successful. In modern times, though, another factor has become crucial to consider due to an increased prevalence of in-unit electronic devices: electromagnetic interference.
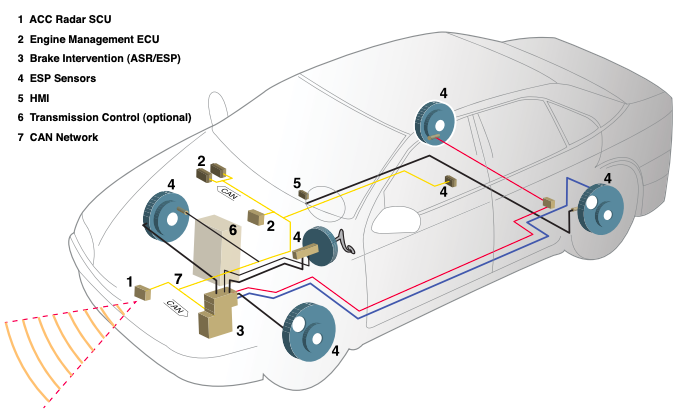
Image Source: Orbel
EMI Shielding in Automobiles
Count the number of electronic devices operating within your vehicle at any given time. Chances are, you’ve got a handful of electronics (and probably some that you don’t even know about) functioning behind the scenes to accomplish one of the most magical, nostalgic experiences in America: driving a car.
When on the road, it might not seem like there’s much happening within the vehicle aside from what it takes to drive the car in the first place. Factor in the radio, though. Then, the navigation. Then, the heat warmers, the electric windows, the lights, the Bluetooth… the list goes on. Each of these products is products of complex electronic systems that enable what we love about driving to become possible.
They also exert forces that we can’t even see nor hear – ones that have the potential to severely impact the overall functionality of the vehicle itself. Electromagnetic waves operating against each other can tamper with each other’s systems, resulting in irreversible failure and potential danger for drivers and passengers. For this reason, compatible and reliable EMI shielding within automobiles is hugely important.
Digital circuitry within electronics generates electromagnetic interference, and the emission becomes stronger when components like overlapping wires or printed circuit boards are involved. Another concern is EMI generated outside of the vehicle, such as in a cellphone tower.
Electromagnetic interference can come from anywhere in many strengths, so it’s essential that all parts in any electronic system are compatible with one another, especially in instances like automotive applications where safety is involved. Most car manufacturers specify a minimum 200 v/m immunity level to protect in-car electronic systems from other sources of interference.
Designing for Protection: EMI Shielding
There are several industry-standard techniques used to protect EMI shielding using custom-designed models to combat interference in different regions of the electronic’s operating system. More times than not, more than one technique will be used to ensure full protection. The most common techniques include the IC level, printed circuit board level, module/enclosure level and interconnect level.
When addressing noise-related interference, the IC is a safe bet to start with, as it is generally the source of noise. Chip manufacturers are focusing on fixing this issue by using spread-spectrum clock techniques, adding ground planes, and using internal decoupling capacitors at the chip level to improve its EMI.
The printed circuit board level requires techniques such as partitioning, board stackup, vias isolation, and routing. Accurate techniques are needed as early as when components are placed on the board. Critical circuits and functions need to be assembled closely to have the shortest trace lengths. So, it is recommended to use multilayer boards with many ground planes. High-speed traces can become transmission lines. For filtering components, place jumpers or “zero-ohm resistors” can hold their place. Real components can be added later, only if testing proves necessary.
The module or enclosure level is considered to be an expensive technique. However, board-level shields and conductive fabrics can help lower the cost. Sheet metal, for example, provides several hundreds of dB attenuation. But the amount of leakages from apertures is what really determines shielding capability. This is where gasket selection and the type of environment becomes important.
In the interconnect level, cables can become weak due to weight and cost issues. It is not as simple as adding shielding to the hundreds of feet of wire harnesses in vehicles. This would cause a huge weight penalty and be a bit expensive. The best approach is to add filter components at the board I/O interface.
K.R. Anderson’s custom fabrication process means engineered solutions crafted just for your applications. We offer effective EMI / RFI shielding. To learn more, get in touch with our experts.