Thermal Interface Materials
KraFAB’s thermally conductive materials that reduce air gaps from electronic devices by conforming uneven rough mating surfaces. There is a wide variety of fabricated films, wet dispensed thermal materials and pad thermal interface materials to fit your application.
Thermal interface materials (TIMs) are materials that go into joints to fill air gaps between solid surfaces during assembly.
Many electronic devices use fans and heat sinks to keep the temperatures cool, but TIMs play a critical role in assisting with the displacement of heat.
The heat generated by individual power devices, integrated circuits, and within complete electronic systems has increased radically in the last decade. The need for thermal management systems is essential to preserve electronic systems operating within their specification. Peak performance and reliability depend on proper temperature limits sustained by thermal management systems.
What happens during assembly?
When surfaces are attached with an interface, there is most commonly an area of mechanical contact at the interface sight. This is due to the surface roughness or waviness and will have an impact on the heat conduction. The surface irregularity and the resulting gap is the primary cause of thermal contact resistance as the gaps fill with low thermal conductivity air. To minimize the resistance, filler materials are generally required to increase the contact between the mating surfaces.
Typically, several interfaces exist between the heat generating element and the eventual heatsink.
The thickness can vary from a few thousandths of an inch to several hundredths of an inch. Some of these consist of permanent bonds like solder or adhesives.
Other interfaces are non-permanent and will form part of the heat transfer path, such as a component being bolted to a heatsink or between an assembled module and a chassis.
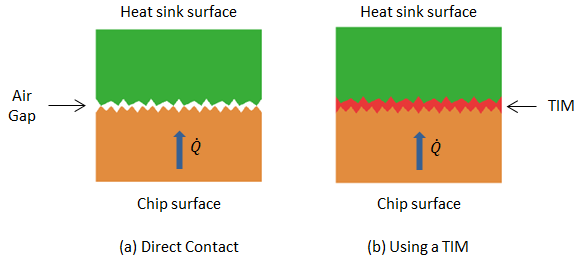
Image Source: MyHeatSinks
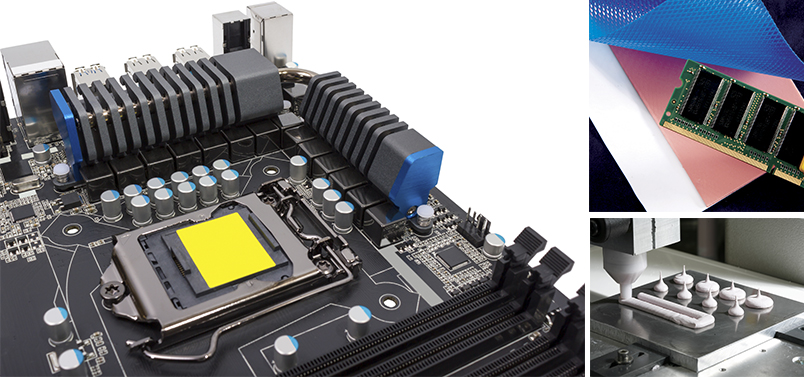
Some of the thermal interface materials used to transfer heat from electronic devices includes:
- Dielectric pads
- Heat spreaders
- Thermal compounds
- Thermal Gel
- Thermal tapes
- Phase change materials
- Gap pads
- Thermal greases
7 Types of Thermal Interface Materials for your Application
We offer 7 top options through Parker Chromerics designed to meet your manufacturing needs. Each has its own features adapted for different use cases.
1. Gap Filler Pads
One of the most commonly used formats is gap fillers.
Several decades ago, fillers were created as a logical follow to dielectric pads. These materials are designed to be soft, thermally conductive, and electrically isolating to fill a variety of interface areas (or “gaps”) and aid in heat removal.
Pads come in a variety of conductivity, softness, and price points. A PSA version is offered on several products offering permanent attachment while others have a natural tack that offers aid in assembly and manufacturing.
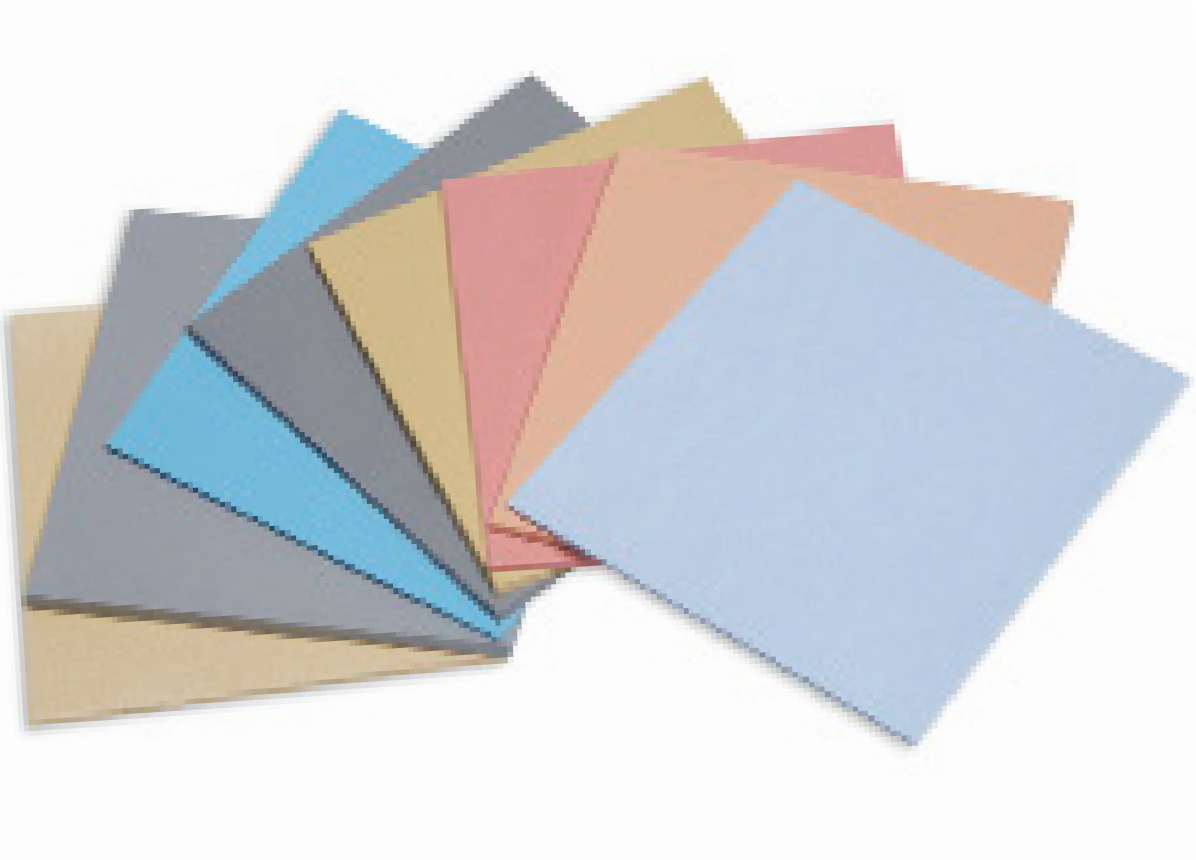
Gap fillers are generally quite soft, but they are not compressible and instead deflect under load. So, if the jointed areas are out of flat or parallel, significant force may be required to get the entire jointed area wetted.
Most commonly, gap filler pads are made from filled silicone elastomer. Like all elastomers, gap fillers will take a compression set. This may necessitate replacement if the system is disassembled and re-assembled.
Benefits:
- Ultra low deflection force
- High thermal conductivity
- High tack surface reduces contact resistance
- Custom configurations available.
New exciting materials from Chomerics
- Parker Chomerics THERM-A-GAP PAD 30 Thermally Conductive Gap Filler Pads provide a soft (34 Shore 00) solution with 3.2 W/m-K of thermal conductivity.
- Parker Chomerics THERM-A-GAP™ PAD 60 Thermally Conductive Gap Filler Pad is a soft, high performance thermal gap filler pad with 6.0 W/m-K and a Shore 00 hardness of 31.
Our most popular gap filler pads are
- Chomerics THERM-A-GAP families of gap fillers. They are available in a wide variety of formats including multiple carrier options, with or without PSA, and thicknesses, etc. Each of these families has unique advantages in terms of thermal conductivity, softness, and price point.
- THERM-A-GAP HCS10G provides an ultra-low hardness solution (4 Shore 00) 1.0 W/m-K.
- THERM-A-GAP 569 is a very low hardness solution (10 Shore 00) with a 1.5 W/m-K thermal conductivity.
- THERM-A-GAP 579 is a low hardness solution (30 Shore 00) at 3.0 W/m-K with the lowest outgassing.
2. Gap Filler Gels
These gels are very similar to their gap filler pad predecessors.
The difference, however, is that these thermal interface materials are dispensed into place. These are not pads with PSA, these are pre-cured single-component compounds applied directly.
Gap filler gels allow for very large compression ranges with minimal compression force. This results in an extremely well-wetted joint with little stress on the joint surfaces. It offers the conformability of curable compounds but with a much better shelf life.
Benefits:
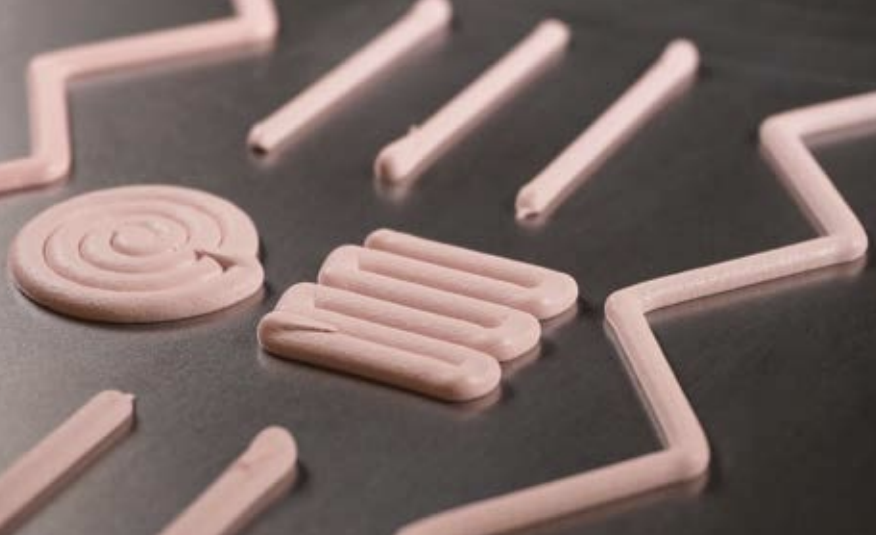
- Dispensable
- Fully cured
- Highly conformable at low pressures
- No refrigeration, mixing or filler settling issues in storage
- Single dispensable TIM can eliminate multiple pad part sizes/numbers
- Reworkable
Our most popular gap filler gels are
- THERM-A-GAP GEL T630G, T635, and T636 with varying thermal conductivity levels and price points. Learn more from the TDS here.
- THERM-A-GAP TC50 – a one component, dispensable thermal compound providing low thermal impedance at multiple gaps to allow the use of common heat spreaders.
- THERM-A-GAP GEL 75 – dispensable thermal interface material with 7.5 W/m-K thermal conductivity developed to conduct heat from electronics to a heat sink or enclosure.
- THERM-A-GAP GEL 37 – dispensable thermal interface material with 3.7 W/m-K thermal conductivity and a flowable paste-like texture.
- THERM-A-GAP GEL30 and GEL8010 have been successful in many automotive Electronic Control Units (ECU’s), Power supplies, Semiconductors, and beyond.
- THERM-A-GAP GEL30 is a readily available single-component, fully cured, dispensable gel with 3.5 W/m-k Thermal Conductivity. The low thermal impedance allows for use of common heat spreaders.
- THERM-A-GAP GEL8010 is also a single-component, fully cured, dispensable gel with 3.0 W/m-k that allows for a thin bond line.
3. Dielectric Pads
These pads were the original TIM gap filler pad.
This type of thermal interface material has proliferated in almost an industry where electronics are used. Because of their high demand, they are offered in a wide range of thermal conductivity and dielectric abilities. These materials have good to very good thermal conductivity, but they do require large joining forces to achieve their rated thermal impedance numbers. Most thermally conductive dielectric pads are available with PSA on one side to allow for easier manufacturing.
Dielectric pads are only available in the 5 – 15 mil thick range and due to their relatively hard nature, they are used in either small size joints or very robust larger joints.
Benefits:
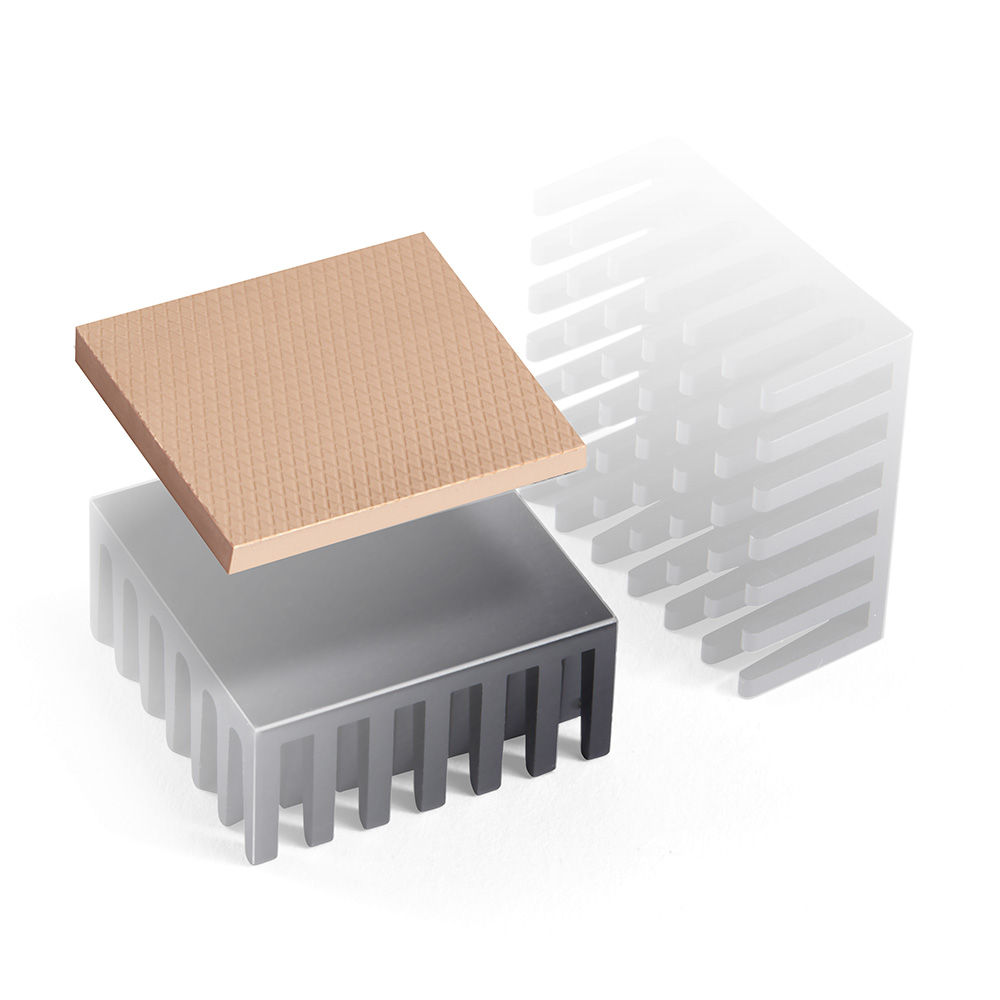
- Excellent mechanical strength and puncture resistance
- Available with & without acrylic PSA
- UL recognized V-0 flammability rating
- Extremely low NASA outgassing
- Proven through decades of use in demanding military and aerospace applications
- Custom configurations available
Our most popular dielectric materials are
- CHO-THERM 500 is a tried and true excellent solution for applications where the highest possible thermal, dielectric, and mechanical properties are required.
- CHO-THERM 1671 is ideal for aerospace and defense applications due to its high reliability and 2.6W/m-k.
4. Curable Compounds
These materials allow for easy fill of almost any joint area.
This even includes gaps as small as 5 mil. They are used in applications where a typical gap pad might be used but where no compression forces are available. They are also used in underfill, overfill, and potting applications.
Some curable compounds offer moderate adhesion properties as well. Curable compound TIMs also have a side benefit of shock and vibration damping.
These materials do require some practice in order to effect a neat and effective interface. Probably the biggest drawback with curable thermal compounds is the shelf life and storage conditions requirements.
Benefits:
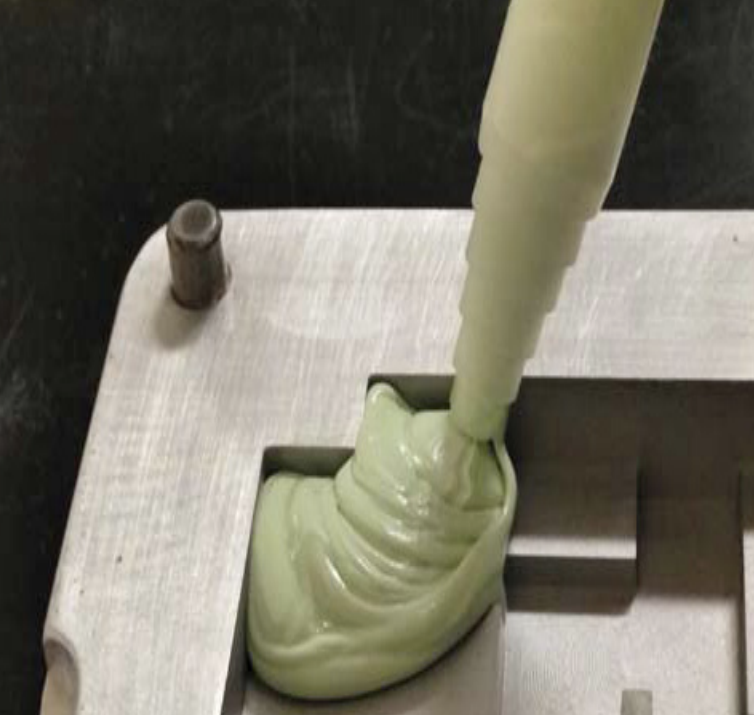
- Cures in place
- Dispensable form-in-place gap filling, potting, sealing, and encapsulating
- Excellent blend of high thermal conductivity, flexibility and ease of use
- Conformable to irregular shapes without excessive force on components
OUR MOST POPULAR CURABLE COMPOUNDS ARE
- THERM-A-FORM T647 is a two-component silicone elastomer with high thermal conductivity (3.0 W/m-k). Due to its low modulus characteristic, it is well suited for elaborate shapes and forms on a PCB and other applications.
- THERM-FORM CIP35 is a versatile two component 3.5 W/m-k thermal compound with a 55 Shore A hardness. Due to its low modulus characteristic, it is well suited for elaborate shapes and forms on a PCB and other applications.
5. Thermal tapes
Tapes have the additional benefit of being an easy to use and low cost thermal and attachment solution.
Double-sided tapes allow for a moderate thermal solution while freeing the designer from allocating space and money for mechanical attachment of the jointed surfaces.
When PSA tapes are used, attention must be paid to jointed surface cleanliness and flatness.
Benefits:
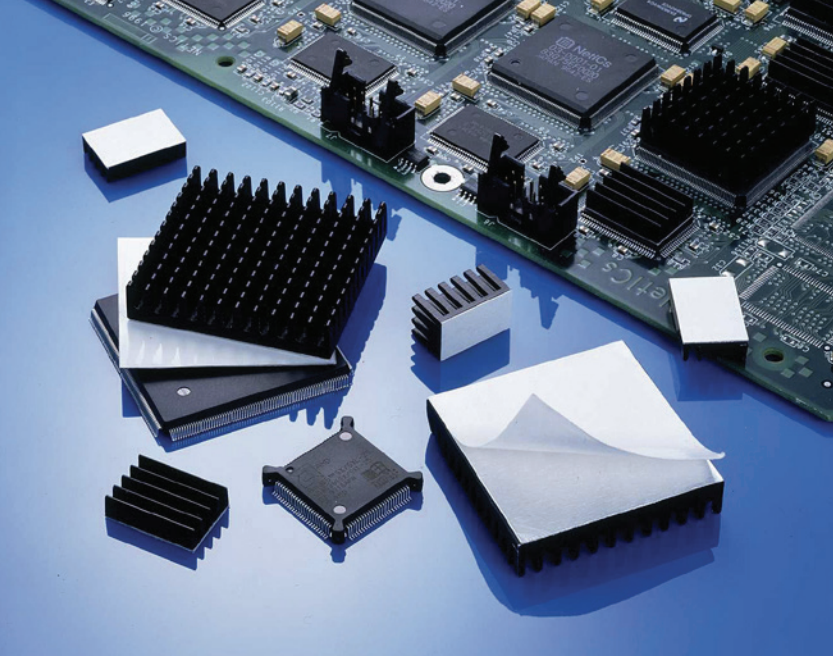
- Offered in various forms to provide thermal, dielectric, and flame retardant properties
- Offered in custom die-cut configurations to suit a variety of applications
- Eliminates the need for mechanical attachment (i.e. screws, clips, rivets, fasteners)
Our most popular PSA tapes are
- Chomerics T418, T412 and T404 respectively focus on adhesion, thermal conductivity, and electrical isolation.
6. Greases
A good choice for their very low thermal impedance.
Lower end thermal greases can be a low-cost thermal interface solution. The highest performing greases can be quite expensive.
Due to their low viscosity nature, greases are very good for filling very thin interface areas. Greases are not suitable for gaps larger than about 5 mils.
Another possible issue with greases is their inherent messiness. A common disadvantage of thermal grease is pump-out as a result of jointed surface CTE and thermal cycling. This can be unsightly or even harmful in some applications. Also, some greases are subject to drying, which reduces their ability to maintain the thermal solution over time.
Benefits:
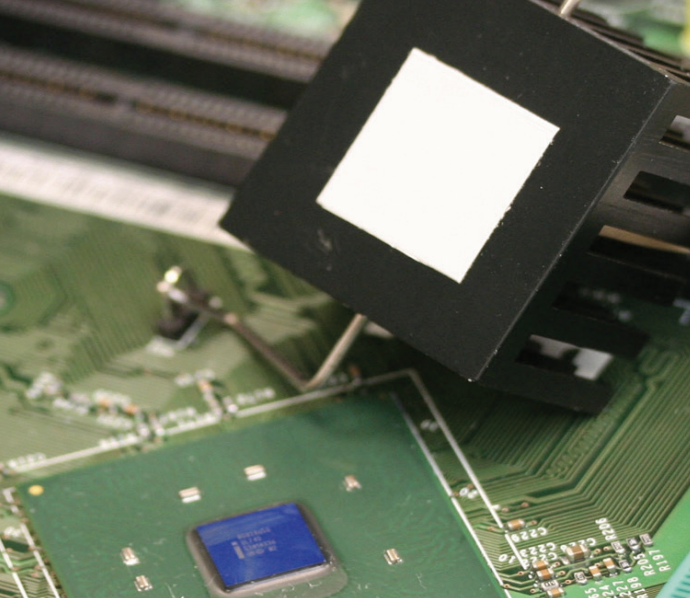
- Silicone based materials conduct heat between a hot component and a heat sink or enclosure
- Fills interface variable tolerances in electronics assemblies and heat sink applications
- Dispensable, highly conformable materials require no cure cycle
OUR MOST POPULAR THERMAL GREASE IS
- Chomerics T670 addresses drying issues with a formulation that will not dry out throughout the entire system life cycle.
7. Phase change materials
Introduced a few decades ago as a potential improvement to thermal greases.
It comes in pad form and melts at typical electronics operating temperatures. This allows for a good thin joint fill similar to the grease format, but without the potential mess and waste.
Some potential drawbacks of phase change TIMs are the fact that they don’t achieve their full thermal potential until they soften and have a flow rate. Because of this, the joint fasteners either need to be tightened during the first thermal cycle or they need to provide dynamic loading.
Benefits:
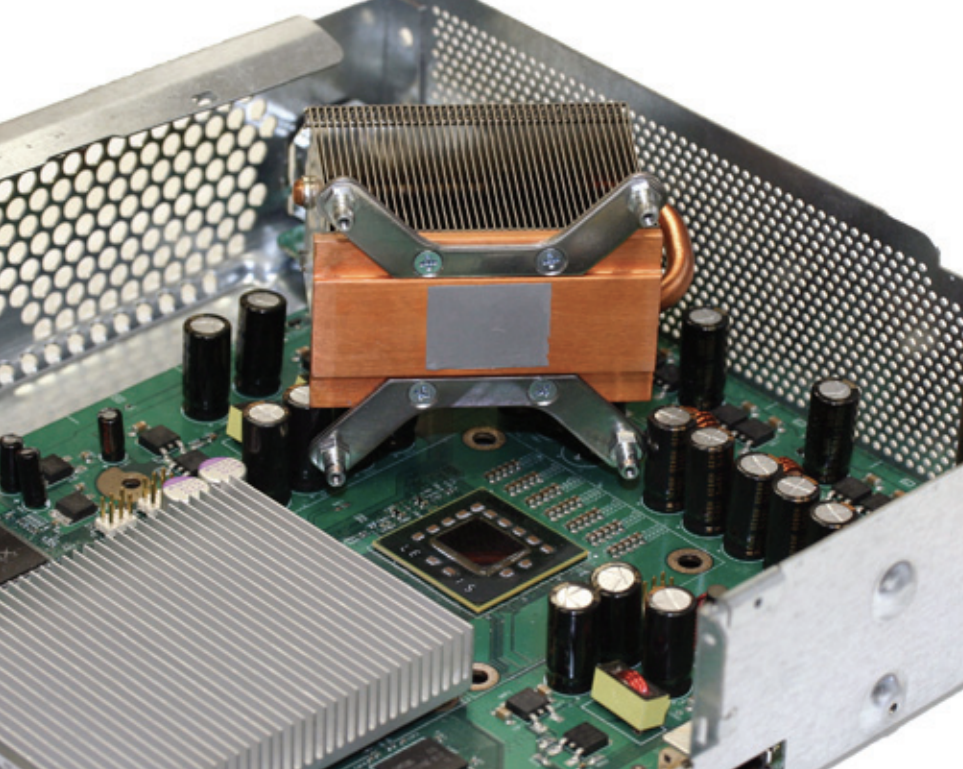
- Low thermal impedance
- Proven solution – years of production use in personal computer OEM applications
- Demonstrated reliability through thermal cycling and accelerated age testing
Our most popular phase change materials
- Chomerics THERMFLOW line and T777 is a very popular phase change choice and offers the same performance levels as a high-end grease.
- T766 and T558 phase change materials add an additional benefit of a clean separation when the joint is dis-assembled via a very thing conformable foil layer on one side of the phase change pad.
We can meet the demands of your electronic designs
TIMs Features
While it improves heat transfer across the interface, it also accounts for most of the total system thermal resistance. Many characteristics must be considered when choosing the best one:
1. Thermal conductivity
Conductivity determines how much heat it can transfer across the interface. This has a major impact on its thermal performance.
2. Electrical conductivity
Some TIMs are electrically conductive but they are generally polymers or polymers filled with non-conductive materials.
3. Phase Change Temperature
This is the temperature at which the interface material transitions softens in order to fill the gaps and to expel all air. It is important that the phase change temperature is below the maximum operating temperature so that heat can be transferred across the interface. The temperature also needs to be as high the device can tolerate, however, to avoid a phase change during shipping.
4. Surface Finish
The efficiency of a TIM to fill large gaps in irregular surfaces is an important factor in material choice. The interaction of filler particles with the adjoining surfaces influences the level of compaction at the interfaces.
5. Mechanical Properties
TIMs in paste or liquid needs to be dispensed or printed. A higher filler volume fraction increases thermal conductivity but also makes it more difficult to dispense due to the increased viscosity.
6. Ease of Application and Installation
The ease of application of a thermal interface material is based on the material and the controlled amount applied.
7. Outgassing
The release of volatile gasses when materials are exposed to elevated temperatures and/or low atmospheric pressures is outgassing. Outgassing is a particular concern in aerospace applications due to reduced pressures and can also cause issues within sealed cavity packages.
8. Pressure
A significant difference in the thermal interface material used is based on mounting pressure. Minimizing contact resistance requires considering TIM performance and the ability to conform to surfaces.
9. Long Term Stability
TIMs need to perform consistently throughout the lifespan of the device. Electronic devices are designed to last seven to ten years, while avionics and telecommunication devices can survive decades.
Reliability of TIMs
The ideal TIMs have high thermal conductivity, require small contact pressure, have no leakage from the interface, do not deteriorate, and are easy to apply and remove. When selecting a reliable thermal interface material, several factors must be considered:
Thermal Conductivity and Bond Line Thickness
Thermal conductivity should be considered, but also the possibility of degradation when exposed to harsh environments over long periods of time. Low bond line thickness is often targeted and requires TIMs with low viscosity.
Thermal Contact Resistance
Low thermal contact resistance can be achieved when the TIM has good wetting with the surfaces.
Adhesive Strength
Reworkability and shock/vibration reliability are reliant on the adhesive strength, especially over temperature ranges. Resilience to stress needs to be considered. A TIM with a high adhesive strength may cause deformation during rework.
Evaluation
Delamination or cracking can take place in a thermal interface material during shock or vibration. Damage to the TIM will result in increased thermal impedance. While visual inspection for damage is needed, the thermal performance must also be tested for reliability. Although a test performed on the electronic assembly before and after shock does not precisely determine thermal impedance change, it does determine if the TIM’s performance will remain within acceptable reliability levels.