Form-In-Place Gaskets Superior accuracy and reliability for even the most intricate gasket designs
What is a Form-In-Place Gasket?
Form-in-place gaskets (FIP gaskets) are thick liquids dispensed on top of substrates to create a strong, durable seal between two surfaces like metal, glass, or plastics. FIP gasket seals offer complete contact with good compressibility, low compression set, and ensure years of effective EMI shielding and environmental sealing performance.
How do FIP Gaskets Work?
A three-axis gasket application process dispenses precisely positioned, conformable gaskets in a variety of cross-sections with an infinite number of layouts. This automated process offers the additional benefit of allowing for batch-to-batch part variations without any tooling changes.
Automation of FIP Gaskets Improves Efficiency and Consistency
This is favorable for manufacturers as it can help meet customer demand. Many years ago dispensing was done manually, thus limiting production and increasing room for error on the assembly line while driving up costs. Today, many robotically dispensed FIP gasket applications provide the lowest total installed cost, reducing it up to 60% over other gasketing solutions. Thus helping save on materials, reducing the space needed, and avoiding expensive gasket production tooling costs.FIP
Conductive Gaskets and EMI Shielding Gaskets
For EMI shielding gaskets applications, a variety of electrically conductive particles can be added to the gasketing compound allowing for shielding effectiveness ranges from 60 dB to more than 100 dB+ at 200 MHz to 12 GHz.
The many benefits of Form In Place Gasketing
FIP Gasketing includes:
- Up to 60% space saved
- Up to 100 dB shielding effectiveness 200 MHz to 12 GHz with very small gasket beads
- Highly compressible gaskets, ideal for applications with limited available deflection force
- Can be dispensed in complex layouts with short lead times and minimal tooling cost
- Quick turn-around of prototypes and samples with fast and low-cost gasket design changes
Our Automated CNC Multi-Axis Robotic Application Process Offers:
-
- Turnkey gasket adhesion to metal, glass, or plastics
- Very small beads with 100 Db shielding
- Complex layouts with short lead times and minimal tooling
Application of Form-In-Place Gaskets: How it Works
Placement of the form-in-place gasket is done by multiple-axis robotic dispensing driven by a CAD drawing of the part. This process ensures reliable sealing against environmental variables and better mating of conductive surfaces.
This application method also allows us to meet varying height requirements and compensate for uneven surfaces in molded parts and castings to provide consistent, highly reliable (with the option for highly conductive) seals.
There are several combinations of elastomers and particles that provide a range of desired properties including compression force, deflection range, electrical conductivity, shielding effectiveness, galvanic corrosion resistance, adhesion and cure options.
Through this process small seals can be accurately placed in complex patterns to meet the increasing demands of electronic enclosure designs. The robotic application of fip gaskets not only improves the manufacturing stage, but improves the longevity of such products requiring EMI shielding, highly reliable environmental sealing, or those that involve mating conductive surfaces.
KraFAB is an authorized converter of Parker Chomerics materials

We use the same procedures to apply form in place materials as Chomerics. Finished products are certified by an authorized distributor. This type of certification is important for some customers with higher standards for quality, especially in the medical and aerospace industries.
Form-In-Place Gaskets
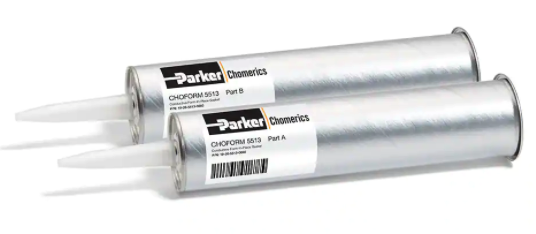
Chomerics CHOFORM 5513
Two-component, thermal cure silicone system, which requires a minimum cure of 30 minutes at 140°C (284°F). The Ag/Cu particle filler makes 5513 a > 70 dB shielding material while also having the best adhesion to chromate coated aluminum and most other substrates.
Product type: Thermal
Tensile strength: 2.4
Operating features: Excellent electrical properties and adhesion

Chomerics CHOFORM 5528
One-component, room temperature, moisture cure silicone system, which requires a full cure of 24 hours at 50% relative humidity. The Ag/Cu filler makes 5528 a >70 dB shielding material, while providing a soft, low closure force gasket.
Product type: Moisture
Tensile strength: 0.86
Operating features: Soft, low-closure force
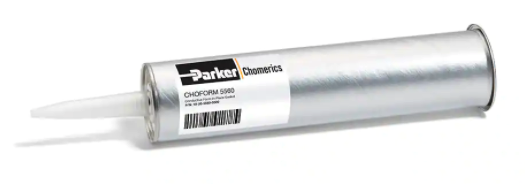
Chomerics CHOFORM 5560
One-component, thermal cure silicone system, which requires a minimum cure of 30 minutes at 150°C (302°F). The Ni/Al filler makes 5560 a very good >90 dB shielding material while also providing the best galvanic corrosion-resistant gasket when mated with aluminum for even the harshest salt/spray fog environments.
Product type: Thermal
Tensile strength: 1.1
Operating features: Excellent corrosion resistance on Aluminum
Gasketing Material Selection
There are several combinations of elastomer compounds and particle fillers that provide a range of desired gasket properties.
Material choices are available for optimization of the material for best shielding, compressibility or available compression, galvanic corrosion, environmental sealing or chemical resistance. In some cases, two materials may be used to create a dual bead gasket that addresses multiple areas of concern.
With a wide variety of gasketing materials, IC packages and EMI Shielding, KraFAB supplies custom materials that have the capabilities beyond that of standard EMI shielding and gasketing. Our custom fabricated materials are developed specifically to meet the demands in a variety of industries.
Our skilled team can help with the selection of a FIP compound to best meet your gasket design requirements and limitations, addressing not only the factors listed above but also allowable gasket envelope, available deflection ranges, and substrate properties as well.
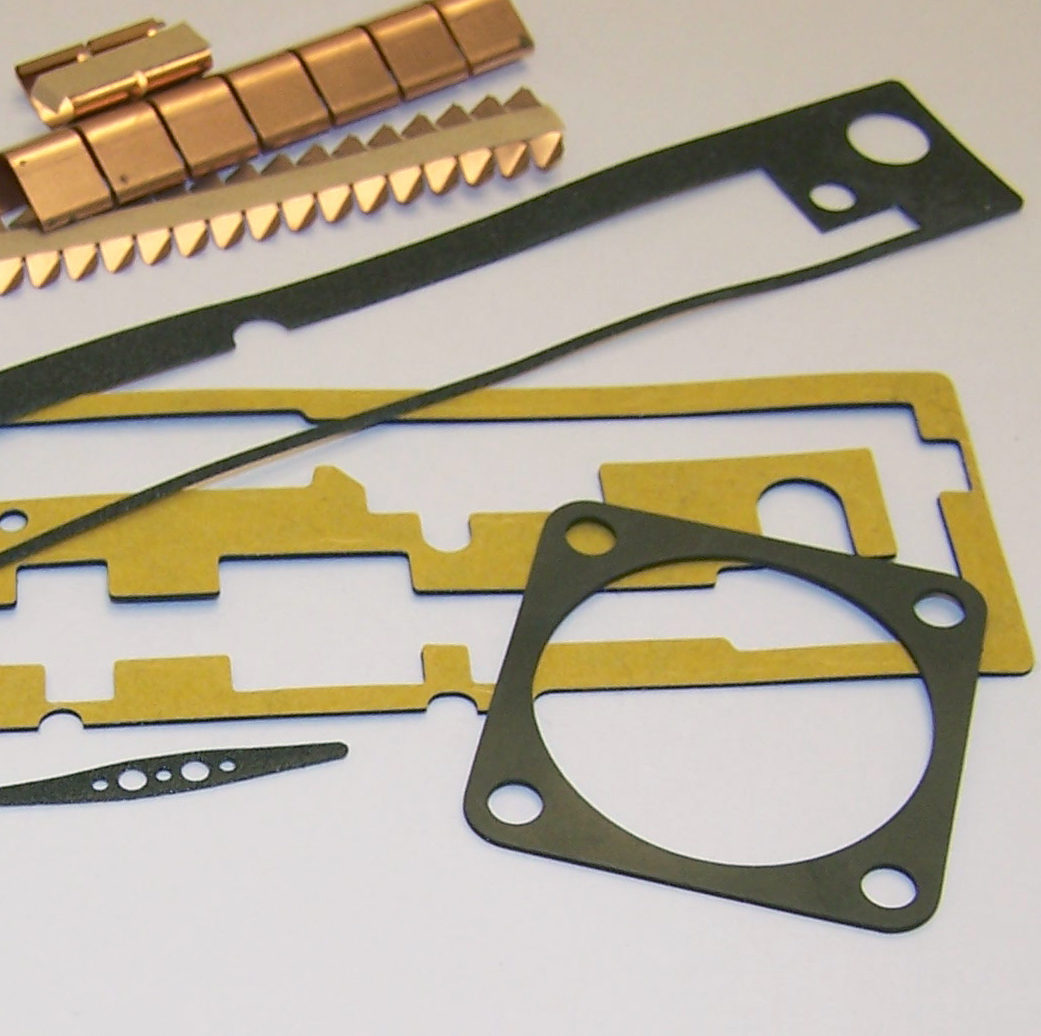
EMI/RFI Shielding
Many electronic devices are subject to a variety of not only environmental conditions but electromagnetic/radio frequency interference.
In densely populated electronics packaging, particularly where intercompartmental isolation is required to separate processing and signal generating functions, conductive form-in-place gaskets provide excellent electrical contact to mating conductive surfaces including printed circuit board traces.
Design Limitations and Considerations
While FIP gaskets are applicable to a significant variety production needs, it’s helping to consider the following:
- Substrate dimensional considerations
- Substrate surface quality considerations
- Packaging
- Gasket adhesion
- Gasket aspect ratios
- Published specs versus real world results
- FIP Gaskets Production
- Quality Control
Our robust and mature ISO 9001 certified quality system plays a key role in ensuring that each customer’s needs for high performing and repeatable gasket solutions are always met.
Each batch of customer supplied FIP substrates is checked for suitability for gasketing, including its cleanliness, uniformity, and damage. Substrates are inspected during the gasketing process as well.
Quality Control of Form-In-Place Gaskets Bead Paths
We have the capability to perform automated dimensional verification of gasket bead placement and height for statistical process control, using a fully programmable optical coordinate measuring technology and vision systems. Electrical resistance of cured gasket material is tested using a 4-probe multimeter capable of measuring to 0.001 ohm in conjunction with custom apparatus designed for testing FIP EMI gaskets. Typical Cp and Cpk values for most FIP gasket application processes are approximately 1.5.
Rapid Prototyping of FIP Gaskets
Since this installation is dependent primarily on software and programming, it permits rapid and inexpensive prototyping, production scale-up and design changes. It works well for batch runs or continuous production, from ten to ten million parts.
Through our latest generation form-in-place gasket application, metal, plastic, and glass surfaces and enclosures are sealed against moisture, air, dust, liquids, gaseous substances, dirt and EMI/RFI interference. By implementing in-line curing of the FIP gaskets, production times are cut and turn-arounds are increased.
We can further reduce production and sourcing costs by adding secondary EMI products, thermal interface materials, PSA’s, damping foams, labelling, marking, protective films and packaging to create a turnkey production solution.
Industries Using Form-In-Place Gaskets
FIP gasketing has become a widely accepted sealing and shielding solution over the past 2 decades across all manufacturing industries. Its unique value proposition of low cost and high performance has made it one of the first choices for engineers looking for shielding and sealing solutions.
It has been used in telecom, military, aerospace, industrial, transportation, life sciences and commercial EMI shielding and sealing applications to replace molded, extruded, die-cut gaskets and RTV sealants for decades.
Tell Us About Your Project
Contact K. R. Anderson for design and manufacturing engineering support. We are one of the original Authorized Chomerics Distributor, Fabricator, and Form-In-Place gasket Application Centers in the United States.
Gasketing Production
Packaging
The most common problems that occur when a product is in-transit can be mitigated through proper packaging. There are four key areas to focus on in order to decrease damage when wrapping, packaging, and shipping FIP gaskets.
- Proximity. The longer the distance, the greater the chance for damage.
- Manufacturer-controlled shipping. Placing control in the manufacturer’s hands can decrease overhead costs.
- Stretch wrapping as improper wrapping can make a load much more unsafe and unstable.
- On-site box fabrication. For items that are rarely ordered, custom boxes are not necessary.
The ongoing search for the best ways to help our customers means communicating with our customers about a part, including how it’s unpacked and assembled. Considering these factors allows us to optimally serve customers in the packaging and delivery process.
Offering Quality Form-in-Place Gaskets for Over 20 Years
K.R. Anderson was one of the first companies to offer automated FIP gaskets technology back in 1997. Today, our company has installed form-in-place gaskets solutions for customers across the globe in almost every industry imaginable.
Our automated form-in-place gaskets system is ideal for EMI shielding, environmental sealing applications, or both simultaneously. Our automated process takes the guesswork out of working with uneven surfaces, conductive surfaces, and especially high complexity gasket designs.
Form-In-Place Gaskets are Optimal for Various Substrates and Designs
Our precision FIP gaskets application works on almost any substrate design and construction. It can be applied directly on castings, machined metal, or plastic, providing turnkey assembly. For quality sealing and shielding at a low cost, reach out to us today!
Other KraFAB Services Include:
Technical Info on Form-In-Place Gaskets From our engineering team
What is From-In-Place Gasketing?
A form-in-place gasket is created by dispensing an uncured polymer compound through a needle and down onto a lid, cover or other housing component in a gasket “bead”. This bead is then cured to create an elastomeric gasket. This gasket and housing assembly will later be mechanically joined (or “flanged”) to another in order to achieve an environmental seal or to complete an electromagnetic interference (EMI) shield or both. For the purposes of this guide we will refer to any surface onto which an FIP gasket may be applied as a ”substrate.”
How do FIP Gaskets Work?
FIP gaskets are dispensed using precision CNC machines. Typically, these are three (or sometimes four) axis robots. In some cases a commercially available CNC dispensing robot can be used for this purpose, but normally a system specifically configured for FIP gasket application is required to repeatedly create good quality gaskets.
Historical Development
FIP technology got its start in the 1970s in the automotive industry as a less-costly alternative to traditional die-cut, molded or extruded gasket solutions. Like many modern formulations, these first FIP material were moisture cured silicones (also known as room temperature cure or room temperature vulcanized (RTV)) compounds much like familiar home use caulking compounds. Over time heat cure compounds were developed as well.
Today there are also a number of other catalyst cured silicones and a few UV cured FIP gasket systems. Finally, there are a few fluorosilicone, urethane and acrylic compounds that have been used FIP gaskets as well. Due to the many advantages of FIP gasketing (as will be detailed below) its use has gone far beyond just the automotive industry and has now spread through almost every industry and market imaginable. One very important development in the work of FIP gasket was the blending of conductive powders (or “fillers”) into the base compound. This allowed for a new form of conductive elastomer EMI shielding gaskets.
Work with a team Backed by Decades of Industry Experience
We can guide you toward the most cost-efficient, easily fabricable product on the market.
Experts ready to help you identify considerations pertinent to your choice of one system
Introduction to FIP Gasket Design Considerations
As would be expected for any design, there are many considerations regarding an FIP gasket, the surfaces it touches and the system as a whole.
One of the first things engineers often think about is gasket sizing. For starters, available FIP gasket dispensing systems can only dispense a gasket that is well under 0.100 in. (2.54mm) tall. It is possible to make two passes where the second gasket is stacked on top of the first to allow for a taller net gasket height. For many applications, this arrangement works well, but it does result in a gasket that is more susceptible to shear.
With this knowledge in hand, the designer has a rough initial go/no go criteria in deciding whether or not FIP gasketing might the applicable to a given application. If the application would traditionally use a thick gasket (like a cabinet door), you can be pretty sure that this is not a good FIP gasket application.
An FIP gasket will always be wider than it is tall. That “aspect ratio” can vary from 0.7 – 0.85 depending on the material and how much it is friction sheared by the dispensing system. As the gasket height is very important in determining how will the system is sealed or how effectively it shields, by default engineers need to design around the height and incorporate any necessary gasket width into the design. Actually, designers can save some QC time for their company if the mark the FIP gasket width as “reference only” in drawings as this dimension is pretty much irrelevant as long as the gasket height is correct.
The above discussion does not address the more recent availability of FIP gaskets filled with nickel bearing powders that are shaped prior to curing using a magnetic field. This process allows for a gasket with an aspect ratio greater than 1. However, these gaskets are still relatively small in cross sectional area.
The above discussion also does not address “Foam-in-Place” gasketing. This is a form in place system specifically designed to dispense a polymer that will foam at the dispense point to create a D shaped gasket profile. This is a specialty gasketing system which is very expensive and is used to make gaskets around 0.100 in. and taller. As such, this sort of system is used exclusively in high volume (typically automotive) applications.
When thinking about gasket sizing one must also think about how much compression the gasket will see when it is fastened between the two flanged surfaces. Gasket compression is normally measured as the compression distance over the nominal original height of the gasket expressed as a percentage.
When You Should Use FIP Gaskets (and When You Should Not)
1. FIP gaskets can be created with very small cross sections. This feature potentially frees up space in the assembly that would not be available with a cut sheet stock gasket. In some cases the gasket flange can be as small as 0.025 in. (0.76 mm). Another benefit here is that a smaller gasket requires less material. For high cost compounds (particularly those that contain precious metal fillers) that reduction in material used can be significant – especially when compared to all the waste that occurs when cutting gaskets from sheet stock.
2. The narrow width of FIP gaskets along with their D shaped profile and relatively soft cured hardness, can offer better joining of out of flat or out of parallel flanges than flatter and/or wider gasketing systems (like extruded or sheet stock gaskets). This potential benefit (again) may offer less material cost and assembly area dedicated to gasketing. It may also allow for fewer and/or smaller fasteners. This may allow for thinner, lighter flanges as well.
3. Because FIP gasketing is done using a CNC dispensing system and the tooling cost and lead time required is either nil or relatively small, rapid prototyping, changes in design, and production scale-ups are very easy to accomplish relative to other gasketing systems. Although each job change does require some machine set up, the small amount of time required for this means that small batch runs are doable at a reasonable cost. For larger runs, many FIP dispensing systems can be set up for multi-part dispensing cycles as well as automated throughput.
4. Complex multicavity gaskets are easily generated using FIP gasket technology. This FIP gasketing benefit is mostly applicable to EMI shielding applications where assemblies usually have very dense component populations, very limited space between components and many of them must be isolated. However, this feature sometimes a very useful environmental sealing applications as well.
One can achieve this same result with a custom molded or injection molded gasket solution. Molded gasketing technologies offer the best possible performance available. However, this technology demands very complicated and expensive parts and tooling and requires very long lead times to get to a working solution.
One could also possibly create a complex multicavity gasket solution with a cut extrusion or some other type of gasket, but achieving this with one of these other methods is normally going to be extremely time consuming, offer a lower performing solution and will ultimately be more expensive.
5. FIP gaskets offer adequate to good adhesion to common housing substrates and coatings.
This statement requires the caveat that “good adhesion” is a rather subjective phrase. First, virtually all manufacturers make some kind of claim about the adhesion of their FIP gasket materials. Some manufacturers test FIP gasket adhesion with proprietary test methods. Others use standardized test methods, but these tests are subject to interpretation, modification and/or errors. Some manufacturers do not offer any information about how they evaluate adhesion. Therefore, one should not rule in or rule out an FIP compound based solely on a manufacturer’s sales or test data literature. Second, the substrate surface for a given application and the gasket bead width (i.e. the area of attachment for the gasket) play a very large role in the strength of the gasket bond. Third, how the gasketed assembly will be treated from the time it arrives at the customer site until the assembly is at the end of its life is an important consideration in deciding if an FIP gasket offers adhesion adequate to the needs of the application.
The best way to look at FIP gaskets is that they complete a sealing and/ or shielding solution when properly compressed between flanged surfaces. In the current state of the art this gasketing system is not designed for any kind of shear forces. If considering FIP gaskets for an application, the specifier should source a an adequate quantity of FIP gasketed prototype parts so an assessment of suitability can be made.
6. FIP gaskets are self-attached to the assembly. This feature obviates the need to design methods gasket attachment as well as sourcing materials and assembly space for same. Since FIP gasketed assemblies arrive on the manufacturing floor complete. Any labor associated with installing gaskets on site is removed.
This benefit of FIP gasketing does require a bit of disclaim as 1) there is the obvious cost of sourcing a substrate with the gasket pre-installed, and 2) FIP gasketed assemblies do require some care in packaging and handling that might not be needed in a more traditionally gasketed assembly
7. FIP gaskets utilizing conductive particle fillers can achieve shielding effectiveness of more than 100 dB from 200 MHz to 12 GHz. This type of performance is not guaranteed as every application presents unique characteristics. It is hard to beat the shielding capability of a highly conductive sheet stock gasket sandwiched between wide and flat flanges with plenty of fasteners. But, for narrow EMI gasket installations with complex bead path geometries, FIP gaskets are usually a great performance and cost solution.
Using FIP Gaskets to save money (and other economic considerations)
The array of options spans from custom-molded to insert-molded gaskets, each with distinctive requirements and constraints. The decision-making process must carefully consider these factors to ensure a balance between performance requirements and practical limitations.
-
Custom molded gaskets – this solution requires one or more expensive tools with long lead times. Also, these gaskets must be attached to the substrate. This might be very costly and/or time consuming or just plain impossible in some applications.
-
Insert molded gaskets – This technology requires a very expensive tool, and the substrate must be designed to work with this process. Lead time to commission the molding tool is usually very long and iterative. This process is generally only suitable smaller substrates (in the range of 40 or 50 square inches or less) due to machine limitations and tooling costs.
-
Extrusion – This process requires some method of gasket attachment, Often the substrate is designed for a gasket groove which occupies valuable package space. Pressure sensitive adhesive (PSA) is sometimes and option, but this is not possible with very narrow profiles. Regardless of method of attachment, this is a very painstaking and costly assembly in installations with complex geometries.
-
Cut foam or rubber sheet stock – This solution is feasible for simple geometries and gasket widths of around 0.100 in. (3.9mm) or wider. Putting a multi-cavity cut sheet into an assembly can be very challenging especially if the wall widths are narrow. This solution requires design and implementation of an attachment method and generally results in significant material waste as well.
-
Formed metal, knitted wire, conductive foam or fabric over foam gaskets – All of these are good solutions for EMI shielding in the right application, and all of these offer compressibility superior to FIP gaskets (except solid knitted wire profiles), Conductive foam is good for complex gasket geometries as long as the gasket width is not too narrow. None of these offer the ability for use in narrow gasket applications like FIP or molded gaskets. They all require design and implementation of an attachment method and all require manual labor to install (more so as the complexity of the gasket increases).
Inventory costs are reduced as there is no need to maintain stock of pre-manufactured gaskets.
FIP Gasket Applications
Due to the performance advantages listed above, FIP gaskets are used in virtually every industry where sealing or EMI shielding are needed. There are literally tens of thousands of major programs where FIP gasketing technology has been used over the past 4+ decades. It has been largely adopted in virtually every mature industry and it is rapidly finding uses in every nascent industry as well.
Aerospace and Aviation
drones, airplane seats, airport ground equipment, flight instrumentation, flight simulators and battery enclosures
Consumer Electronics
portables, major appliances, IoT devices, entertainment systems and battery enclosures
Industrial Manufacturing
mining and construction
Telecommunication
WiFi routers, cellular point of use devices, cellphone stations and satellites
Automotive and Transportation
mechanical equipment, in cabin enclosure sealing, monitors and controls, accessory and auxiliary systems, drive and power system, logistics tracking, controls and security systems and battery enclosures
Medical
ventilators, oxygenators, heart pumps, infusion pumps, dialysis machines, AED’s and battery enclosures
Defense and Military
radar systems, munitions guidance and control systems, GPS systems, C4 systems including man-portable through theater level equipment, targeting systems, munition defense systems, night vision equipment and battery enclosures
Test & Measurement
bench and portable network analyzers, signal generators, semiconductor, PCB and functional test equipment
Energy – power generation and distribution for both traditional and fossil fuel free systems and end user meters and controls
Tolerances in Gasket Dimensions
The designer should expect a tolerance range of +/-0.004 in. to +/-0.006 in. (+/- 0.01mm to +/- 0.015mm) in gasket height and width along any run. Those values can be expected to double at any locations where the dispense needle starts and stops. It should be noted that with some compounds and some systems tolerance values may be higher. The expanding of tolerance numbers at gasket initiations and terminations may seem like a potential concern. However, in practice because those areas are so small (usually just 0.1 in. (2.54mm) in length) and because the gasket is fairly compressible those expanded tolerances rarely present a problem.
Types of FIP Materials
Common FIP Gasket Compounds
Most FIP gaskets are produced with silicone compounds. There are some fluorosilicone FIP gasket formulations, and occasionally an acrylic or urethane compound will be used for FIP gasketing. To date conductive particle filled FIP compounds are exclusively silicones or fluorosilicones with the vary majority being the former.
The choice of compound is usually driven by the use environment.
Advantages of Silicone – Silicones offer great adhesion, reasonable shelf and pot lives. They are easily compressible so they can seal/shield well. They take fillers well, and they resist UV, moisture, ozone and many other chemistries.
Limitations of Silicone – Some environments will not allow for silicones due to outgassing or oil expression concerns. Flourosilicones are harder to work with and they tend to be more expensive, but they are better in terms of outgassing and oil expression. They tolerate hydrocarbons much better than silicones. Acrylics offer superior adhesion. They tolerate many chemistries very well and have good UV resistance. They are not as good with compression set as silicones however. Urethanes are very strong and offer good adhesion and chemical resistance. But, they are generally harder to use as FIP gaskets than other materials.
The two most common cure methods for FIP compounds are moisture and heat cure.
- Moisture cure FIP gaskets tend to be softer and offer lower substrate adhesion than heat cure gaskets. The moisture cure process is done at room temperature and the gasketed assembly can usually be handled in a few hours. Full cure normally takes from 24 – 72 hours. In very dry environments, moisture curing can be accelerated somewhat by using a humidity booth/tent if the substrate will not be negatively affected by this.
- Heat cure FIP gaskets a typically process at around 150 C (about 300 F) or less for about an hour. Heat cure schedules vary by manufacturer, and some manufacturers offer more than one schedule for a given compound.
There are a few materials suitable for FIP gasketing that use a different catalyzing system or UV light to quickly create a gasket at ambient temperature. This are not very common.
Conductive fillers in FIP gasket compounds can include:
- Silver
- Silver plated copper
- Silver plated nickel
- Silver plated aluminum
- Nickel plated graphite
- Nickel plated aluminum
Pure silver-filled compounds will generally be the most expensive, followed by silver-plated metals. Nickel graphite-filled compounds are generally the lowest cost. Nickel-aluminum fillers are the newest filler option. This type of filler offers some great benefits in corrosion resistance, cost, and shielding stability. While the precious metal fillers offer greater conductivity, graphite fillers sometimes offer better “bite” into conversion-coated substrates due to their “chunky” morphology.
On the topic of galvanic compatibility, this is an important consideration in any EMI gasket application where there is any potential for moisture near the flange. In this instance, any “galvanic mismatch” between joined surfaces presents a risk for galvanic corrosion. While this corrosion is sometimes simply unsightly, it can lead to a loss of shielding or even structural damage. To minimize galvanic corrosion potential the designer needs to pick a an EMI gasketing compound with a filler that is closely matched to the flanged surfaces. Silver bearing fillers are not normally used in these situations because they are a poor galvanic match to just about all materials used to create EMI shielded enclosures.
All uncured FIP compounds have an expiration date (or shelf life). This is typically 1 year and sometimes only 6 months. If the compound is a commonly used one then this of no concern to the customer as the FIP installer will be churning through material well before product expiration occurs. However, if a less common material is selected for an application, the customer may need to consider periodic production volume versus compound shelf life as well as production lead time for the compound.
On the plus side FIP gaskets are very material efficient on a per-installation basis. This includes yield loss considerations as well. So, a little compound goes a long way.
Most FIP compound manufacturers are very conservative in establishing shelf lives. As such, most FIP materials that have been properly stored can be used for quite a while after those dates. Few manufacturers will take on the liability of recertifying expired material, but the customer or installer can run the same QC tests the manufacturer uses to confirm that the material will do the job. If the material’s ability to be dispensed, adhesion, durometer, tensile strength and (for conductive-filled types) volume resistivity are acceptable, the material can continue to used.
Virtually all of the commercially available FiP compounds are compliant with modern environmental protection regulations. When conductive filled FIP compounds expire the metals from them can be reclaimed by a recycler.
Silicone FIP gaskets are okay at best in terms of outgassing. Fluorosilicone or urethane compounds may meet the requirements of low outgassing applications.
Compression Ranges for Unfilled and Filled Silicone FIP Gasket
Factors Impacting Gasket Compression
-
Compression force – a function of fastener size, spacing and the clamping force they generate.
-
Flange stiffness, flatness, and parallelism – will dictate the distribution of that force along the surface of the gasket.
-
Gasket Modulus & Shape – will move at any point of contact under a given compression force.
-
All Applicable Tolerances – All tolerances tweak all values up or down.
For an unfilled silicone FIP gasket a compression range of 10% to 30% is usually pretty good depending on the level of sealing that is desired. If the goal is to prevent air or water penetration under pressure the solution must be tested rigorously as the FIP gasket may not be up to the task. For a filled silicone FIP gasket compression should be targeted at 30% nominal +/- 10%.
Over-Compression and Compression Set
For either an unfilled or filled gasket, one could potentially compress the gasket more without degrading the sealing/shielding solution but the gasket would be ruined. It would either rupture or it would take a very large compression set. The other over-compression phenomena that occurs frequently with silicone gaskets is silicone oil expression. While this oil is inert, its presence may still be a concern depending on the application.
On the topic of compression set – this is a phenomena that occurs with all elastomer gaskets. When compressed within their allowable range most elastomers will show a compression set of 20% – 30% of the original gasket height. If the application requires that the flange is unjoined at some point, the designer should analyze whether or not the now compressed gasket is suitable for one or more additional open – close cycles. While many FIP gasket users subject their gaskets to several open/close cycles with no apparent negative effects, the safest solution is to specify that the gasket always be replaced after it has undergone compression set.
If there is any way to accommodate compression stops into the assembly design, this can often mitigate many concerns about over compression. Rails, grooves, bosses, shoulders on screw fasteners or shims are all worth considering.
Groove Considerations for Shear Protection
If one is considering putting their FIP gasket into a groove there is an additional benefit of extra shear protection for the gasket. However, this is rarely practiced as the groove requires extra machining, a groove takes up valuable package space and the gasket will generally need to be bigger to stay within the target compression range in all tolerance conditions.
Substrate Design for Accurate Gasket Positioning
To allow for accurate and repeatable gasket positioning on the substrate with reasonable application cycle times, the substrate needs to have locating holes and/or edge rails that can be used for registration. Functional substrate through holes are suitable for this purpose. If neither of those are available, the substrate can probably still receive an FIP gasket but the installed cost will be higher than it would be otherwise
Potential Interference from Production Artifacts
Designers need to be aware that die/mold parting lines, mold gates, runners, flash or burrs can interfere with positioning pins, edge rail alignment and/or clamping hardware. Those production artifacts should be avoided, removed or minimized when they may impact the ability to install an FIP gasket economically.
Design Rules for Top Wall Application and Through Hole Registration
In many applications the FIP gasket is applied to the top of a wall (also sometimes called a rib or rail). Depending on the material used that rail could be as narrow as 0.25 in. (0.625mm) wide. It must be noted however that designing a gasket that may over-hang the edge of that wall is not a prudent practice. In doing so there is a large likelihood that gasket would detach at one or more points when put under compression. It might also be dislodged prior to then. It is unlikely that an FIP installer would warrant an installation of that sort. A good rule of thumb to avoid this condition is to ensure that the top or ledge is at least 0.005 in. (0.127mm) wider than the nominal bead width. This restriction applies to any tapped or through holes as well. If a through hole will be used to aid in substrate registration this offset need to be even greater (see next paragraph for more on this). This distance may need to be larger also depending on the FIP material used.
Dispense Needle Clearances and Constraints
FIP gasket compound is dispensed vertically using gravity. So, the dispense needle needs to come down directly over the bead path. In order to do that without crashing into obstacles such as pins, pedestals and walls a minimum of distance of one-half the nominal gasket width + 0.010 in.(0.254mm) must be maintained between any obstacle and the centerline of the gasket bead. This same restriction will apply to any through holes that are to be used for substrate registration.
FIP gaskets can be laid upon sloped surfaces – sometimes as steep as 60% depending on material, the dispensing system and the dimensions of the substrate. In some cases dispensing on a slope will require extensive tooling and/or multiple application cycles which will impact both cost and leadtime. Sometimes it is simply impossible to do this and another gasketing solution (at least locally) must be found.
Substrate Reproducibility Requirements
To create accurate gasket beads, the surface to be gasketed and any surfaces used for substrate registration, must have a part-to-part reproducibility of better than 0.008 in. (0.20 mm) in X and Y dimensions and 0.012 in. (0.30 mm) in the Z dimension. Variations in substrate thickness will cause deviations in the net Z height of the substrate. So, that must be controlled as well to maintain that 0.012 in. Z dimension reproducibility.
Robot Reprogramming for Batch Consistency
For a given batch of parts the robot can be reprogrammed to account for dimensional variation from specifications as long as the entire batch is consistent in that regard. That said the customer should expect delivery delays and increased costs when this needs to be done.
Substrate Warpage and Fixturing Solutions
Sometimes a substrate will exhibit warpage. In a molded part this might be due to non-uniform stress relaxation or shrinkage of the mold material. This condition will present in thin machined metal parts that have endured friction heating during machining. In either case these parts will probably exhibit correct dimensional reproducibility when in a constrained state, but absolute dimensions will not be so when unrestrained.
This warpage means that parallelism and flatness will not be adequate for FIP gasket installation. This issue can often be mitigated with fixtures that constrain the substrate. However, setup and production time will be slowed to accommodate this. If the substrate does not have locations suitable for clamping that won’t interfere with the gasket installation process, more complicated fixturing schemes (along with a further cost and lead time increase) will have to be developed.
Dispensing Robot Coverage Limitations
The area that an FIP dispensing robot can cover is limited by its X and Y travel axes, and the depth it can reach into a part is limited by its Z axis. FIP dispensing robots typically will have dispense areas under 2’ x 2’ (610mm x610mm) and Z axis travel <10 in. (254mm). These limitation dictate the maximum substrate size that a given system can handle (at least in one set up).
Substrate Composition and Surface Finish
Introduction to FIP Gaskets and Substrate Compatibility
Generally, speaking almost any manufacturing material suitable for use as a housing will also be good for an FIP gasket. There are a number of materials or surface finishes to which FIP gaskets do not adhere well. In some cases a primer, etchant or other surface activator can mitigate this problem.
- Substrate Materials Suitable for FIP Gaskets
- Aluminum (ideally with Mil-DTL-5541 Class 3conversion coating)
- Magnesium castings (with surface pickle applied)
- Zinc
- Stainless Steel
- Poly Carbonate
- ABS
These materials can be cast, machined or (in the case of plastics) molded. If the part is cast or molded some thought should be given to the need for ease and repeatability of registering parts under the needle on the robot.
Surface Treatments for FIP Gaskets
- Nickel plating
- Vacuum metallized aluminum
- Paint (including conductive paint)
- Gold plating (very occasionally)
Key Issues with Substrate Composition and Finish
-
Adhesion to nickel for Concerns about conductive FIP gasket compounds
-
If a heat cure FIP material is selected, suitability of a plastic housing, a painted surface (including graphics) or added accessories for the cure cycle
-
If it is an EMI shielding application, picking a conductive FIP compound that is well matched in terms of galvanic compatibility and system shielding effectiveness
Regardless of the substrate surface finish it should arrive at the FIP gasket installer ready for gasket installation. Occasionally, a customer will ask for a bare metal or plastic housing to be gasketed. In those cases the casting, molding, forming or machine house suppling the substrate will need to ensure that there are no oils or mold release on the part. Normally the substrate will come to the installer from a coating, plating or painting facility. By default the entities supplying that service should deliver a part that is ready for FIP gasket. In practice however, some these suppliers produce finished substrates that are not FIP gasket suitable. For example, a conversion coater may produce a coated housings the meets conversion coating specifications, but the chemicals used have impurities that cause the Fip gasket to fail in adhesion.
Handling Non-compliant Substrates
At least several times each year an FIP gasket installer will receive a batch of substrates that are not clean. The cleaning process is not typically a part of the installer’s business as it involves dedicated equipment and specialized materials to do it properly, efficiently and safely. There are typically environment compliance laws and regulations to navigate as well. The best answer is for the substrates to go back to the producer for proper cleaning.
Ad-Hoc Cleaning Measures
If the customer is in a time crunch and is willing to accept an ad hoc cleaning process and the gasket installer is willing and able to do so the housings may often be satisfactorily cleaned where they are.
Pre-Production Validation
If a customer is considering using the substrate cleaning services of a gasket installer offering this as a standard service, this portion of the gasket installation process should be validated prior to entering production to ensure that there are no hiccups with gasket adhesion.
Also, the FIP gasket installer needs to be made aware of what cosmetic standards required for the finished substrate. That way the gasket installer may avoid putting gaskets on a substate what should held for disposition by the customer
Sealing and Shielding Challenges
Occasionally, an application may call for an external environmental seal and an inboard EMI shielding gasket. These applications are always ones where system performance enclosure ruggedness, and longevity is a must. The easy answer for these applications is to use a sealing and shielding solution other than FiP gasketing. However, due to cost, lead time, volume, logistics or other concerns. FIP gaskets are sometimes still used in these applications. Sometimes just one FIP gasket type is used and the other is a different style of gasket. This situation calls for early evaluation of the gasketing solution and it should be covered in detail in a group consisting of the assembly’s end user the assembly design and production staff and potential gasket solution providers.
Hardware Integration Issues
Users of FIP gaskets may face a bit of a conundrum with regards to hardware that must be added to the substrate. It may be difficult to press in pins, fix brackets or ground straps or place other accessories without risking damage to the FIP gasket. Conversely, those items may not be compatible with the FIP gasket installation process – they might interfere with the dispense needle or make registering the part under the needle impossible. Or, they may make packaging a challenge or be subject to damage or loss during packaging, shipping and storage. The best answer to this situation is to bring all the impacted parties together to determine if and how to make these seemingly irreconcilable differences work together.
As noted earlier, FIP gaskets only offer moderate resistance to shear forces, This limitation is worse for moisture cure FIP compounds and for gasket installations on to nickel plated substrates and low surface energy surfaces. It has also been noted that all elastomer gaskets are subject to compression set. Therefore, the packaging for FIP gasketed substrates must protect the gasket from shear and compression. Part of the design process (and subsequent sourcing process) should include development of re-usable packaging which protects the gasket. This could be cardboard, corrugated or plastic trays or dividers or foam, corrugated stand offs. Paper or plastic sheets or bags are not sufficient to protect the FIP gasket from physical damage. Additionally, a wrap or bag (polyethylene or sulphur and lint free paper or the like), should go around the substrate to minimize accumulation of dust or lint on the substrate
Design Considerations for Handling
The designer may want to consider collaborating with his/her production or quality assurance staff to establish policies and procedures for handling FIP gasketed substrates to avoid shear on the gasket and compression on same until time of installation.
Designing sealed and/or shielded housing employing FIP gasket technology is certainly not a trivial process. Balancing conflicting demands of performance, cost, compatibility, reliability and manufacturabilty can seem insurmountable. This is particularly true when first attempting to use this technology. However, there are thousands of customers and tens of thousands of programs where FIP gasketing is being used very successfully every day. Once this technology has been employed in a few program cycles, design standards and practices can be codified so using this system becomes fast, easy and even more cost effective. Your FIP gasket installer should be able to assist to make this process as fast and smooth as possible.
Comparison with other Gasket Types
Form-In-Place Gaskets vs Die-Cut Gaskets
A Form-In-Place Gasket Has Better Mating of Irregular Surfaces – Form-in-place gaskets are another choice besides molded gaskets or die-cut gaskets. This unique type of gasket is able to fill in any irregular spaces or gaps on the substrate. Pre-formed gaskets are not consistently able to adequately fill those gaps, which can make form-in-place gaskets an ideal alternative.
Form-In-Place Gaskets Are Less Expensive and Faster than Traditional Extruded and Molded Gaskets – We program the dispensing system, which means there’s no need to create a mold or steel die. The robotic system also makes it much easier to change from one design to another quickly and at a low cost. Form-in-place gaskets are cured at room temperature or by oven and are ideal for applications that involve opening and closing the door or component. This versatile process can be used on plastics, glass, electronics, and more.
These seamless, poured in place gaskets adhere to one side of the surface. By contrast, with cure-in-place gaskets, the corresponding part is attached and the gasket fills all voids for permanent assembly. While both options require prepared surfaces, there are several benefits to using FIP gaskets over traditional gasket methods. Because form-in-place gaskets utilize an automated system already, you can automate the surface prep process and easily transition to gasketing.
Form-In-Place vs Vulcanized Gaskets
Many are familiar with vulcanized gaskets which are so ubiquitous in the automotive space. FIP gaskets are essentially vulcanized gaskets as well. However, moisture and heat cured FIP gaskets offer properties very different than traditional sulfur cured natural rubber gaskets – these differences may be beneficial or detrimental depending on the particular gasket application in question.
Form-In-Place vs Cure-In-Place Gaskets
FIP gasketing should not be confused with Cure-In-Place (CIP) gasketing. The latter is a gasketing process where an uncured compound (or perhaps a thermoplastic compound) is applied to a substrate and that assembly is then flanged to a mating surface prior to any curing or heating process. CIP gasketing will not be covered in much detail in this guide, but we can say that one should expect this gasketing process to offer advantages and disadvantages versus other gasketing systems which may be worth considering prior to making a decision on a gasketing system.
Commercial and Production Considerations
Other Considerations with FIP Gasketing
Work with a team Backed by Decades of Industry Experience
We can guide you toward the most cost-efficient, easily fabricable product on the market.
Experts ready to help you identify considerations pertinent to your choice of one system