An Application Guide for Form-In-Place Gaskets and Robotically Dispensed Thermal Interface Gels and Compounds
Robotically dispensed form-in-place gaskets are an excellent option to consider when complex gasket geometries, limited sealing real estate, turnkey assembly, low-cost solutions or quick turns are a consideration. Likewise, robotically dispensed thermal interface gels provide advantages for varied pad size and shape installations, turn-key assembly, low-cost solutions or quick turns.
However, some design considerations upfront will enhance the viability of these design solutions as well as helping to speed design completions. The following guidelines combined with K.R. Anderson’s decades of experience in robotic material will make for a robust and speedy gasket or interface design.
Here are the four best practices to use when dispensing form-in-place gasketing and thermal materials:
1. Plan for D shaped gasket bead with an 85% height to width ratio.
A two-pass gasket installation can be made for a taller net gasket height, but this increases install cost and results in a somewhat less robust gasket.
2. Plan for a 20-30% compression of your gasket.
This range of compression allows for best sealing or shielding and will minimize component stress in the assembly and gasket degradation.
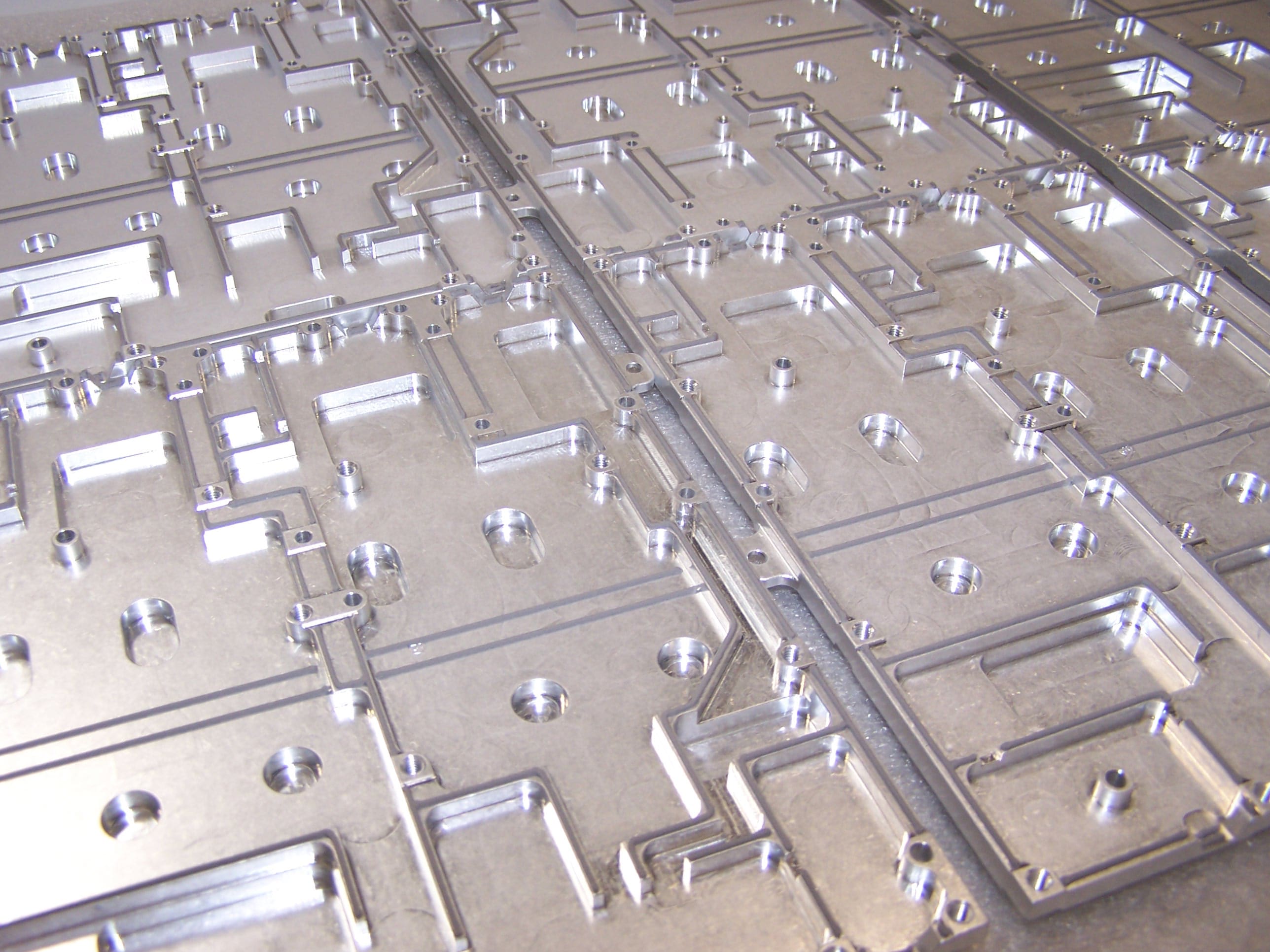
3. Gasket Design Guidelines
Allow space gasket termination and intersection zones. This includes:
The bead path
Should be drawn as outlining the center of the needle’s path.
Vertical Wall or Edge
Starts and stops against a vertical wall or edge of a cliff should terminate ½ bead width + .010” away from the edge.
Terminations
Minimize terminations by maximizing bead path lengths.
T Joints
Minimize “T” joints by running continuous beads around 90° corners.
4. Ensure you’ve chosen the best FIP material for your application.
There are three important factors to consider:
Environmental compatibility
The compatibility of a gasket elastomer and filler can, and will, be dependent on indoor vs. outdoor environments.
Bead Size Range
Allowable bead size range for a given material is determined by conductive filler particle size.
Parameters
Processing parameters for a candidate FIP material can be determined on the applied surface. Heat cured FIP materials allow for faster turn times and slightly stronger adhesion and hardness levels. RTV moisture cure FIP materials, which were introduced for surfaces that cannot withstand an oven cure can be applied to any surface and offer a softer Shore A hardness value.
Here are two considerations for robotically dispensed thermal interface pads:
1. Optimize Performace
Optimize performance and cost by choosing a pad area that will cover a reasonable portion of the area to be sunk. Most of the heat to be conducted away from electronics components comes from the center of the component.
If a few millimeters of the component perimeter are not covered this generally does not affect the thermal solution. Thermal gels and compounds are designed for a huge amount of deflection. Normally for pad areas 1” square or less a simple tall dot of interface material is as good or better than perfectly proportioned square pad.
2. Avoid Air Entrainments
For larger pad geometries work with your pad installation service providers to optimize the dispensed material layout to avoid entrained air under the pad. Every adjacent pair of interface material line in the installed pad present a possible air entrainment issue.