Common Die Cutting Mistakes & How to Avoid Them
The first step in designing a die cut gasket for performance application is to consult an expert. A one-on-one consultation will ensure that the project is done on time, on budget, and according to exact specifications. The first two major mistakes that can be made with die-cut gaskets are covered here.
Let’s now explore 3 more major mistakes to avoid in die-cut design.
Mistake #1 Not Specifying Machining Tolerances
The process of manufacturing a die cut gasket is very different than machining a metal part and requires much wider tolerances. Production techniques, tool type, part features, and material type are all considerations in die cutting techniques.
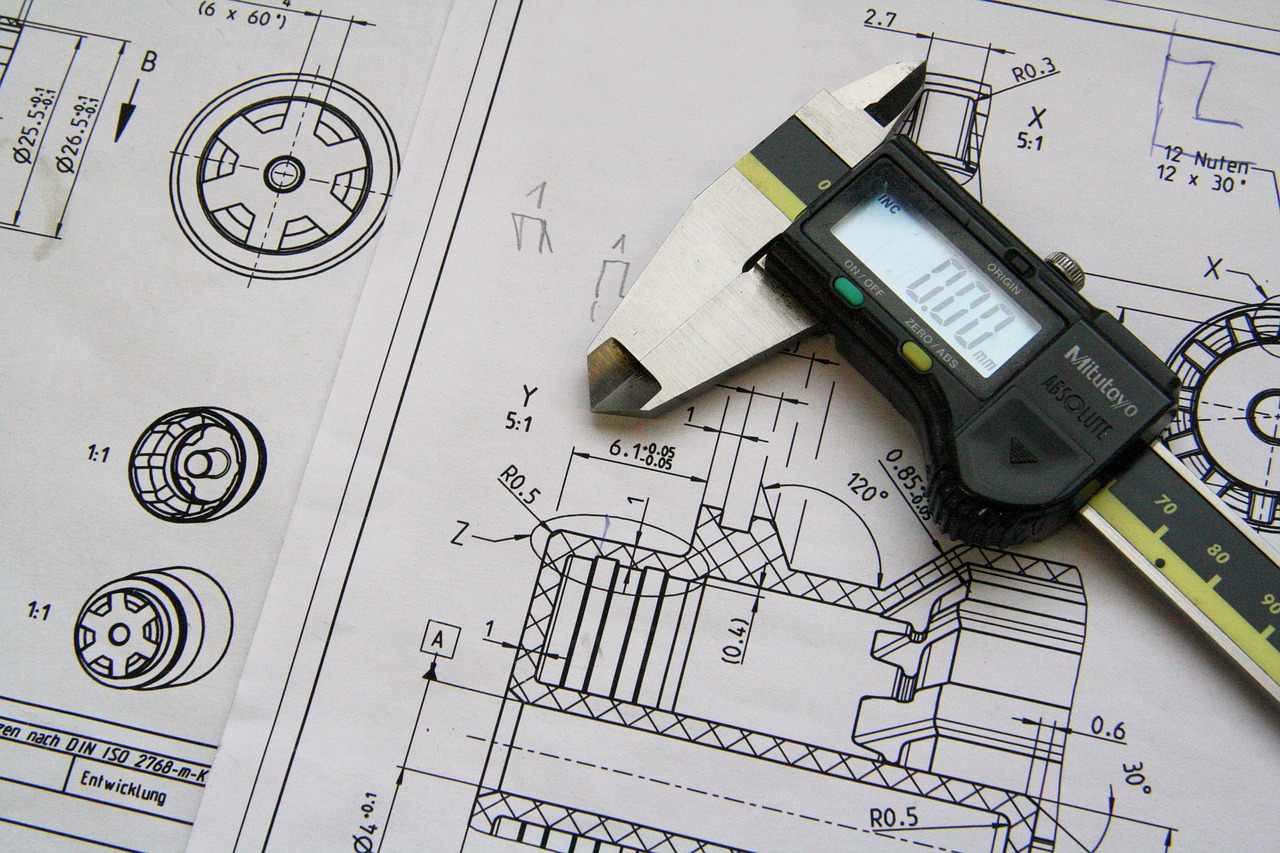
Solution
Tight cut tolerances are best, but an expert must also understand the cutting process and material limitations. An expert in die cutting will consider how to equally match gasket fit, form, and function to processing capabilities.
Top Tip
Tolerance tables are the best way to help engineers correctly specify tolerances. Updating tolerances before beginning production will allow accurate quotes and avoid delays in production.
Mistake #2 Using a Cheap Pressure Sensitive Adhesive (PSA)
In the world of adhesives, not all are created equal. If the wrong adhesive is used, product failure could occur. Be sure to specify the pressure sensitive adhesive (PSA) your gasket converter should use for your application.
Solution
When detailing the specifications for your gasket, choosing the right adhesive is one of the most important design decisions. Temperatures, adhesion strength, and life expectancy are just a few of the vital considerations an expert should think through.
If a private label pressure sensitive adhesive (PSA) is recommended, be sure it will work specifically for your application. Leverage the millions of dollars that some companies have spent on research and development to choose the best adhesive for your project. Even big name brands have cost-effective, high-quality options.
Consider both adhesive surfaces when specifying a PSA. Keep in mind that the adhesive will need to stick to both the mounting surface and the seal.
Top Tips
The main issue with adhesives is to first be sure to specify what type of adhesive you want for your application. Cost, budget goals, bonding limitations, and sealing properties are all considerations when choosing the right pressure sensitive adhesive (PSA) for the job.
Mistake #3 Only Choosing a Die Cut Gasket as a Solution
A die cut gasket is not always the optimal solution. In some gasket manufacturing, up to 75% of the material used ends up being thrown away!
Solution
In order to avoid massive waste, consider a custom molded rubber gasket. If an application is large and irregularly-shaped, an extruded and spliced gasket may be the right choice. For a cost-saving option, form-in-place gaskets can mean fewer assembly line issues when working with thin gasket walls.
Top Tip
Form-in-place gaskets are a great, cost-effective gasket manufacturing method. When working with expensive materials, experts must be especially mindful of alternative manufacturing options.

Conclusion
Your die cut gasket expert is the main resource for avoiding any and all of these mistakes. Walk through all the necessary steps to be sure to meet the specific requirements of your application. Call us today to make KraFAB your die cut expert!