Electromagnetic Interference & Compatibility Measurements
Too often with mechanical, electrical and other software systems, this testing is not a priority, resulting in performance failure. Read on for tips on how to navigate compliance testing for your device.
First, ask yourself the following questions prior to starting a project:
- Has the product undergone compliance testing well in advance of the design process?
- Has proper, prior testing been done to ensure that the product adheres to EMI/EMC regulations?
- Should the product’s release be postponed, what are the potential impacts on cost savings and time?
All things considered, it’s just as important to test your product for EMI/EMC compliance early in the design cycle as it is to test the product’s basic functionality–mechanically, electrically and otherwise. When products aren’t tested, it can lead to serious losses in time and money.
Luckily, advanced testing is available, providing insight into potential risks before even the design process has been completed. Read on to learn more about EMI/EMC pre-compliance testing.
EMI/EMC – The Basics
Electromagnetic interference and electromagnetic compatibility (EMI and EMC) are crucial factors to consider for electronic device manufacturing. When unwanted electromagnetic energy radiates in space or down I/O and power cables, we call this EMI. Any electronic device is capable of emitting unwanted energy, and it’s when that energy causes damage to another electronic device that classifies it as an interference.
Contrarily, when EMI does not damage electronic devices and allows them to function cohesively, we call this EMC. All electronic devices are required to pass EMI/EMC compliance tests prior to going to the market. In doing so, it will be ensured that the device is not damaging–nor can it be damaged–by other devices.
A device must pass the following in order to become EMI/EMC certified:
- Radiated emissions testing
- Conducted emissions testing
- Radiated immunity testing
- Conducted immunity testing
During compliance testing, the unintentional electromagnetic energy emitted from a device is tested to measure emissions. When radiated electromagnetic energy and/or electromagnetic energy conducting down I/O and power cables, unintentional electromagnetic energy escapes the device. WiFi emissions, while intentional, are classified as radiated emissions, meaning that it also must undergo testing to in an effort to ensure that the emissions are being controlled.
Device Immunity
A device’s immunity refers to its susceptibility to interference from other electronic devices. This is especially important to consider in high-technology environments where several different types of electronic devices operate within the same vicinity. Both radiated and conducted electromagnetic emissions (EMI) are capable of damaging electronic devices.
Why EMI?
Proof of EMI/EMC certification is required by Federal law before any electronic device goes to market.
The Federal Communications Commission (FCC) and other organizations created the standards to which electronic devices are held.
Those standards vary depending on the device at hand, especially when testing intentional and unintentional radiated emissions.
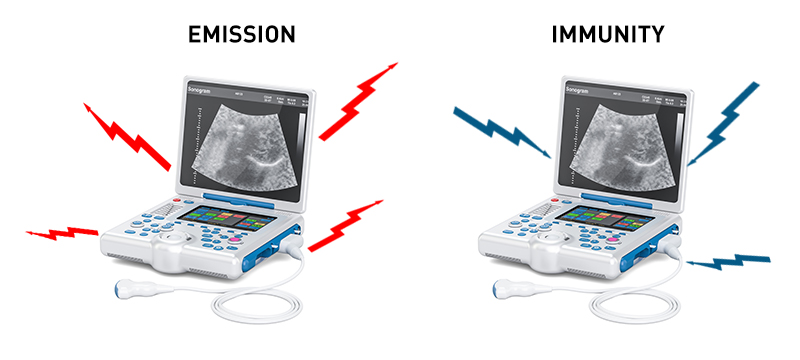
Image source: Parker Chomerics
Regulations for immunity, however, have not been as easily-accepted worldwide. Medical device approval in the US by the Food and Drug Administration (FDA) requires compliance with both emissions and immunity regulations. Countries like Taiwan and Japan are examples of countries that have “country-specific” deviations after having adopted many of the standards, but not all of them.
Recommendations
While EMI/EMC testing can be pricey, it is money well-spent compared to failing compliance tests just before the product is expected to go to market. Once this occurs, it’s nearly impossible to keep the product launch on-track. Again, it’s for this reason that it’s important to complete pre-compliance tests well before sending the device for compliance testing.
As the design cycle progresses, it becomes harder to correct any errors that weren’t caught during pre-compliance testing. If a product cannot be solved at the board level or within a device, a packaging solution will be needed. Due to the subsystems and other internal components of the device, a packaging solution is the easiest way to solve for unwanted emissions later in the design process.
Conclusion
The lack of insight around the emissions of electronic devices’ internal design components can be a roadblock in getting an electronic device to market. Luckily, advanced technology has allowed packaging to be a solution, solving EMI/EMC compliance issues. All things considered, the safest solution is to ensure that pre-compliance testing is completed well in-advance of the design process to avoid any offsets to your project timeline or budget.