Why EMI Shielding Gaskets are the Best for Compression Molding
The most widely-used EMI gasket fabrication technique.
Compression molding is the most reliable and widely-used technique for crafting EMI shielding gaskets. While other techniques are suitable for low-volume production such as prototyping, the compression molding process is efficient, precise and durable when conducted properly – efficient being the most highly-valued characteristic, as engineers continue to search for ways to create more out of less.
Read on to learn more about compression molding and whether or not it’s right for you.
What is Compression Molding?
Compression molding is a manufacturing tactic used to create EMI shielding gaskets using a combination of extreme heat and pressure to mold raw, malleable materials into cutting-edge, industrial-grade products. The compression molding process is durable, reliable and highly-efficient, especially for high-volume production rates.
Compression Molding: How Does it Work?
Compression molds are typically made of strong metals such as aluminum or steel, providing a foundation for the uncured conductive silicone. When the silicone is placed into the mold, it takes less than ten minutes for the mold to form into a rubber-like material.
This standardized molding process creates impeccably precise EMI gaskets time and time again, making it the ideal technique for high-volume, complex gasket manufacturing. Plus, when the mold is removed at the end of the forming process, excess silicone is used to create the next mold. This waste-free process makes compression molding one of the most sustainable and thereby preferential molding tactics used today.
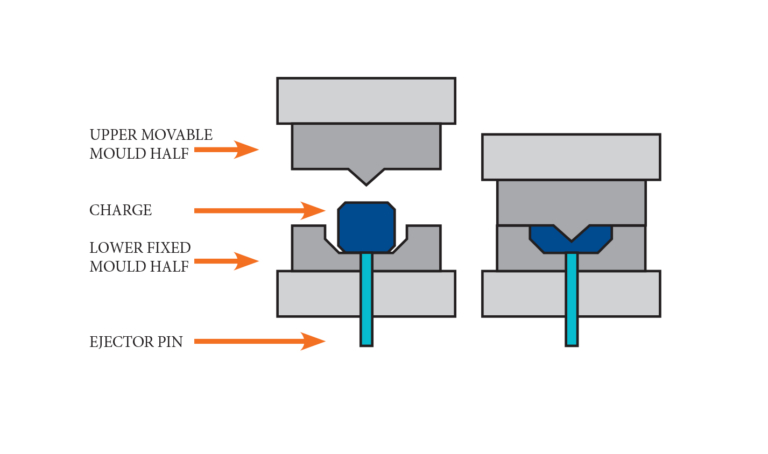
Image Source: dpseals.com
Zero Material Waste Impact
Adopting a zero-waste process can look like saving scraps, but really, you’re saving cost. Scraps add up, and with the cost of many industrial-grade materials being higher than ever, it’s important that nothing goes to waste. Particle-filled conductive silicones help most EMI gaskets to achieve optimal functionality, but some applications require silver or another precious metal due to conductivity metrics, so the price point is subject to fluctuation in the precious metal market. For this reason, molding is one of the most cost-effective and overall efficient techniques used in the industry.
Why Molded EMI Gaskets?
Given the technique’s overall efficiency, the main reason to choose a molded EMI gasket over a die cut gasket comes down to cost savings. Die cut gaskets always produce some amount of waste. No matter how precise the cut is set to be, there’s always a bit left over. That’s why – especially in high-production situations – a molded EMI gasket is preferential for its ability to yield a standardized, precise molding process no matter how complex the design.
Some gasket techniques yield flat, 2-dimensional gaskets. While occasionally functional, these gaskets aren’t entirely complex and could likely be replaced and improved by a three-dimensional (3D) substitute. In this instance, a compression molded gasket would suffice, and is frequently found to be a good alternative to other gasket manufacturing techniques.
Compression molding is time and time again found to be one of the most efficient, effective and reliable EMI gasket molding techniques known in the industry. While some applications might favor another manufacturing process, the molding process consistently yields high-quality, standardized products at impressive volumes. Depending on your needs, compression molding could likely be the solution you need for your next project.