The 4 Best Types of EMI Gaskets Designs
EMI shielding gaskets are designed to create a conductive path between two surfaces. KRA Fab provides EMI gaskets to protect an electronic device and boosts its performance. In order for the electrical conductivity to be reliable and solid, EMI shielding gaskets are essential. Perhaps now more than ever, it is needed to prevent the transmission of interference that inhibits or destroys circuits.
While traditional metal housing may be adequate for the flexibility needed in a design, EMI protection may require the use of shielding silicones. Shielding silicones filled with metal-coated particles meet tough shielding requirements while also providing environmental sealing. KRA Fab gaskets can also be manufactured to the exact shape and size according to design specifications.
When deciding on the best EMI shielding for each design, learn the advantages and limitations of each. The four types of EMI shielding gaskets are cut, extruded, molded, and form-in-place (FIP).
Cut Gaskets
Cut gaskets seal between two surfaces using compression created by sufficient bolt load, which also fills any imperfections on the mating surface. KRA Fab can cut out extremely precise gaskets. Once the exact design specifications are set, cutting can quickly and effectively produce a large quantity.
Cutting also supports both nested parts and any design that requires punched holes or slots with specific radii for fasteners. A conductive pressure-sensitive adhesive backing (PSA) can also be applied to die cuts. This eliminates the need for liquid adhesives on the assembly line, which can often be difficult to control. The gasket can also be kiss-cut, which reduces production time since it eliminates the need for personnel to peel a liner off the PSA.
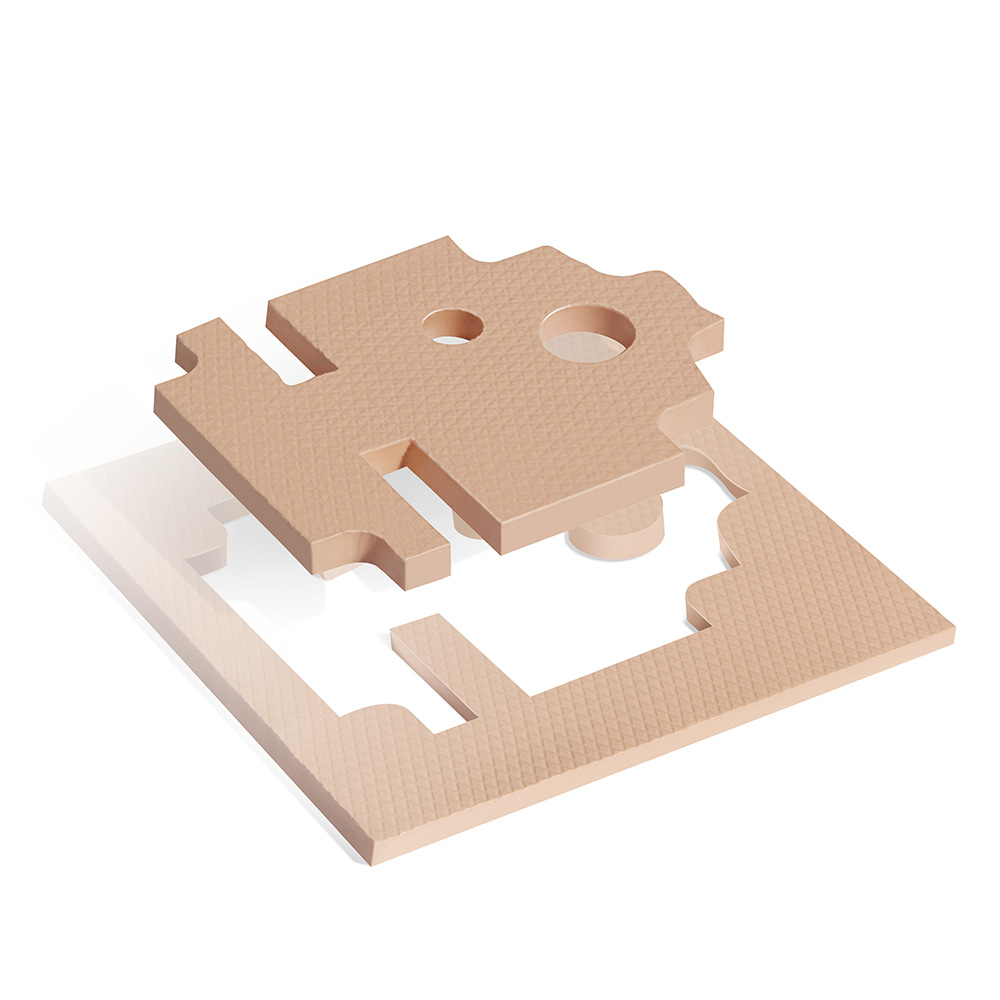
Benefits of die-cutting? Its low cost to setup. Manual material feeding has greatly diminished due to the rise of automation, making the rotary or flatbed equipment much easier to use. The former is best for low-volume orders — especially for prototyping or low-demand products. The latter is best for high-volume orders, as it holds tighter tolerances that are ideal for kiss cutting, improving overall quality of the parts. Vision systems in machines support part alignment and registration, increasing accuracy while greatly cutting down costs and waste.
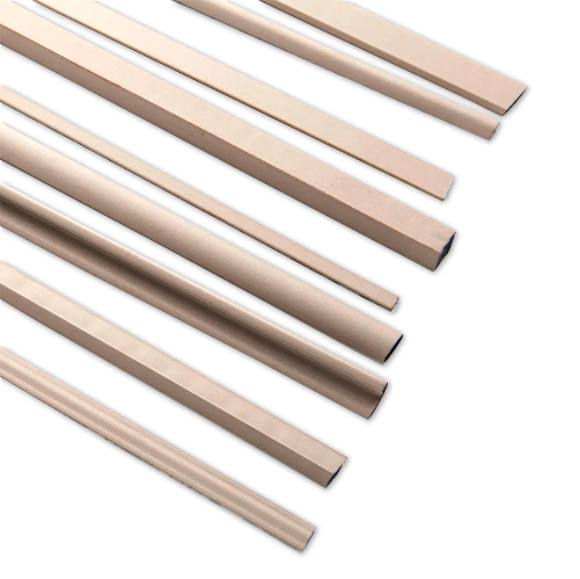
Extruded Gaskets
The biggest benefit of extrusion is the efficient use of expensive shielding materials and the ability to make custom cross sections to meet complex designs.
KRA Fab extruded gaskets can be cut and spliced to exact specifications after curing. This allows for full EMI shielding enclosure seals. Splicing can be done on a small molding press, cold bonded, or glued.
Flange and groove applications are best suited for extruded gaskets. There are a range of profiles available to meet every design requirement. If a custom gasket shape is needed, KRA Fab can use innovative anti-stretch and press-fit features for any project.
Custom Molded Gaskets
Molded EMI shielding gaskets have numerous advantages over die cut and extruded gaskets. The most noticeable benefit is the ability to conform to three-dimensional designs. The flexibility in design, however, can be more expensive. This requires budgeting for additional tooling costs and longer lead times.
While die cut and extruded gaskets are ideal for most jobs, a perfectly conformed design must be custom molded. Custom molding an EMI gasket is an effective way to eliminate the drop waste associated with die cutting. Attention to cost is especially important in custom design due to the need for electrically conductive silicone materials as opposed to standard silicone gaskets.
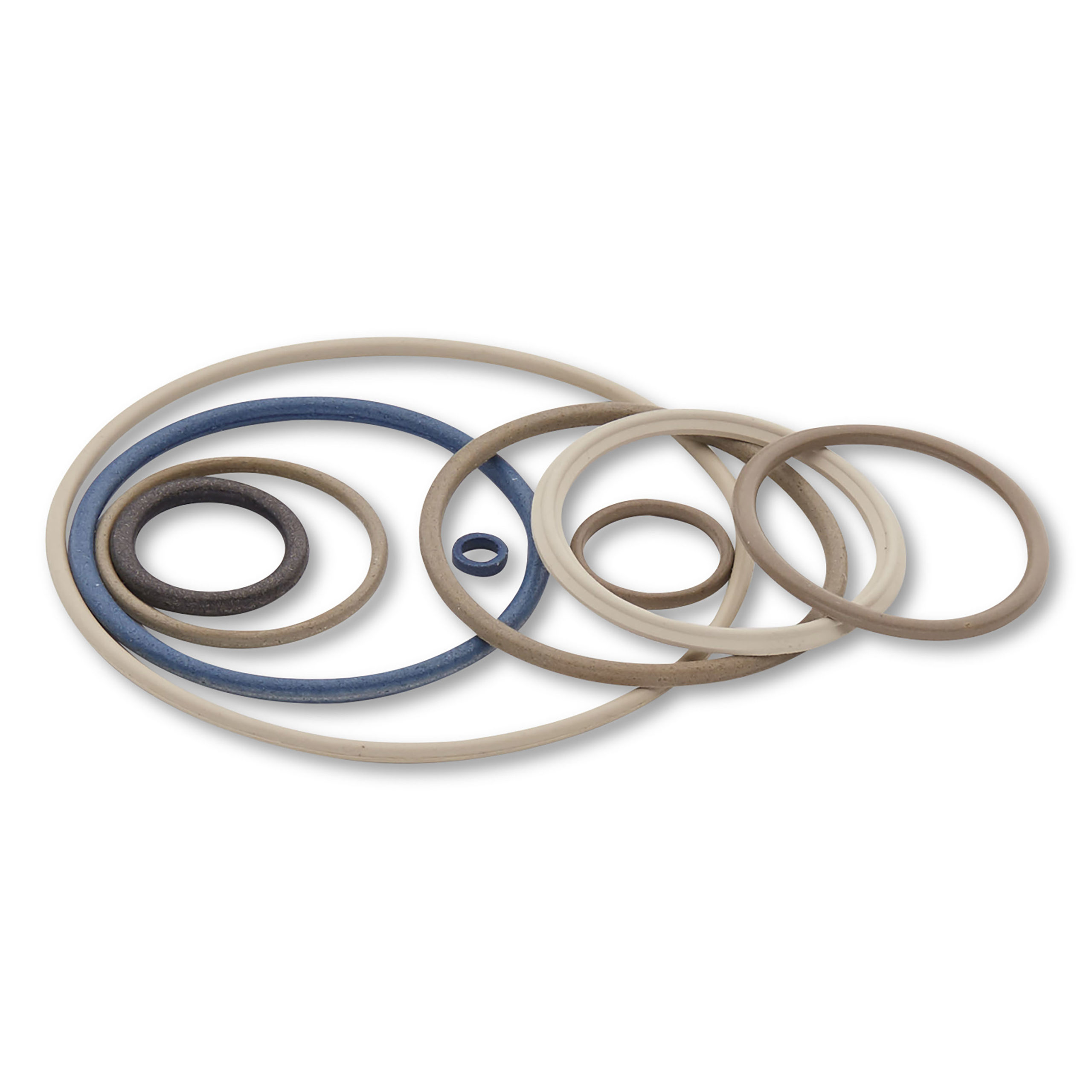
Although cost is a factor, KRA Fab custom molded gaskets do offer unparalleled manufacturing speed and precision. This means that there is very little material waste and that the process can be automated in large volume applications.

Form-in-Place Gaskets
The form-in-place process dispenses a specified profile of electrically conductive silicone onto the substrate. This type of gasket has a low compression force and excellent shielding properties.
Form-in-place gaskets easily accommodate densely populated electronic packaging in situations where complex cross-section patterns and isolation are required. FIP’s also have superior flexibility for gap closure and require no assembly or adhesive.
FIP gaskets are ideal for complex designs due to the automated dispensing methods and efficient use of materials. Programmed machines dispense beads on thin gasket shelves, eliminating manual placement and allowing for compact designs.
Form-in-place gaskets are ideal for applications with available deflection force and have extremely high shielding effectiveness. KRA Fab uses automated equipment to match the exact specifications of the assembly.
KRA Fab EMI Shielding Gaskets
KRA Fab’s experienced team will help you chose which EMI shielding gasket is the best fit for your design. They will show you the most reliable and cost-effective manufacturing processes for all your EMI shielding applications. Work with the experts at KRA Fab today.