PREMIER (™) Electrically Conductive Plastics
Unlike normal plastics, electrically conductive plastics have the ability to conduct electricity — providing “immunity” for sensitive components from incoming electromagnetic interference (EMI) and/or prevent excessive emissions of EMI to other susceptible equipment.
Product designers and engineers are discovering the unique advantages of electrically conductive plastics compared to traditional metals – such as weight reduction, cost reductions, elimination of secondary manufacturing steps – all resulting in leaner supply chains and better products.
Why Conductive Plastics?
Parker Chomerics PREMIER ‘single pellet’ electrically conductive plastic pellets offer superior performance and consistency when compared to many conductive plastic materials. The primary advantage of PREMIER is the use of pultrusion compounding to ensure uniform amounts of conductive filler are within each pellet.
Our PREMIER electrically conductive plastics are manufactured as single pellet formulations, which ensures the most reliable, consistent shielding of molded products.
Single pellet or homogeneous products are far superior to multi-pellet blends (also called dry blends or salt-and-pepper blends) that use pellets from different compounds randomly mixed together.
EMI Shielding Consistency from Part-to-Part
Conductive plastic single pellet performance benefits are easily demonstrated when shielding performance is compared between dry blend materials and PREMIER single pellets in capability studies. Our single pellet materials prevent the risk of poor EMI shielding – and this avoids potential failure in the field.
✔ PREMIER SINGLE PELLETS
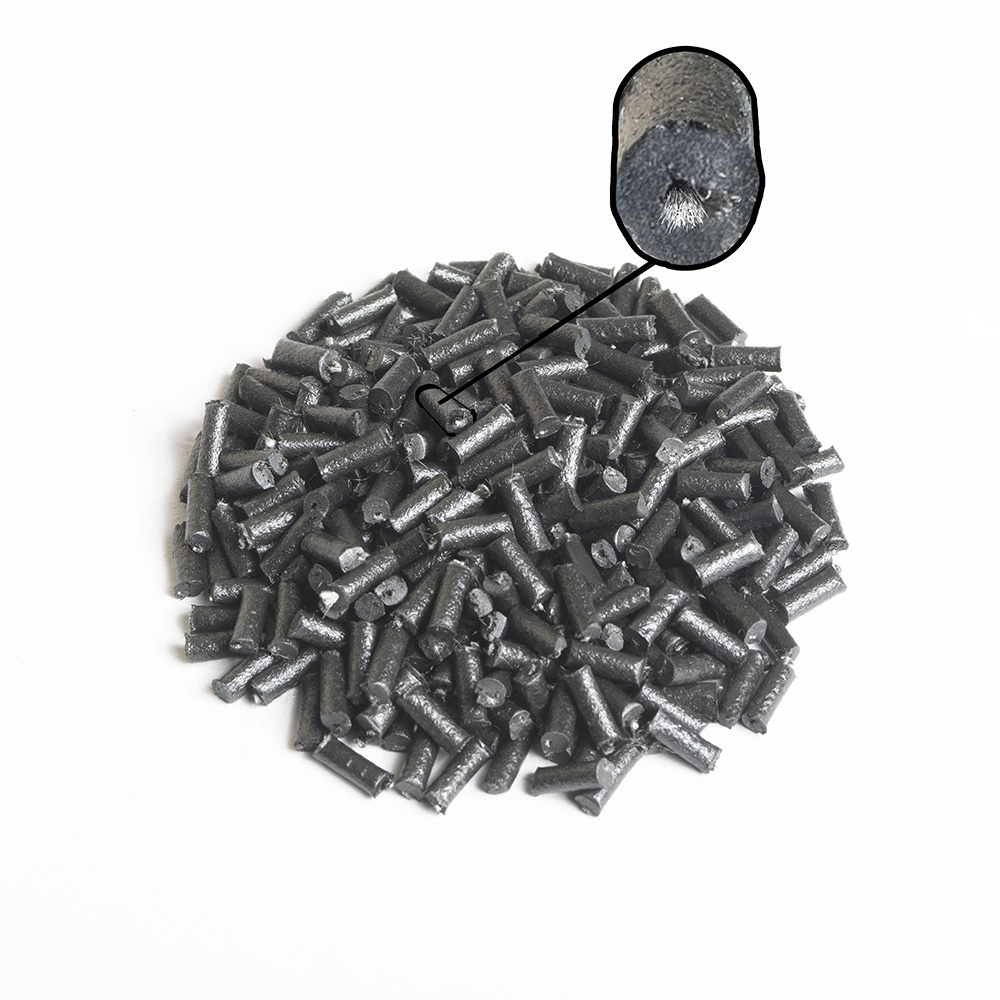
Single electrically conductive fiber in every pellet leads to consistent EMI shielding performance.
✘ MULTI-PELLET BLENDS

Non-homogenous mix of conductive slugs and plastic pellets leads to uneven EMI shielding performance.
Electrically Conductive Plastic Options
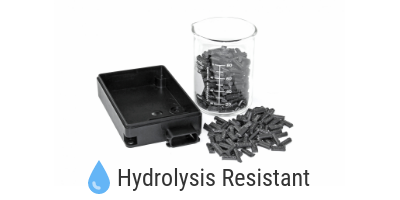
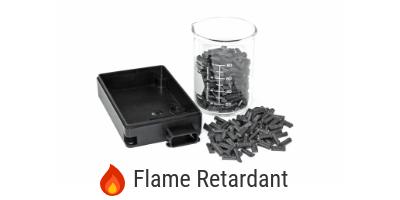
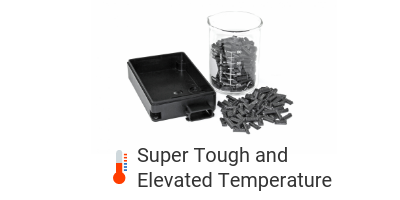
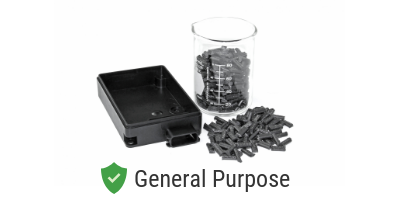
No Packaging Size Limitations
Dry blends (that use multiple pellet mixtures) have packaging limitations – they are sold only in smaller bags or containers, and carry the risk of the heavier pellets settling during transportation.
When settling occurs, it results in inconsistency in shielding and mechanical performance. Large volume programs can save significant labor hours by using single pellet products such as PREMIER.
Up to 75% Less Mass
Our conductive plastics have a density of 1.2 to 1.4 g/cc, which is nearly one-half the density of aluminum (2.7 g/cc).
Conductive plastics offer light weight, coupled with the ability to mold thinner walls, allowing parts to weigh up to 75% less.
PBT and PEI CONDUCTIVE PLASTIC GRADES
PBT is known for its excellent chemical resistance thereby making it an ideal material for environments that have exposure to automotive type fluids (gasoline, motor oil, glycol 50/50 mix, brake and transmission fluids).
PEI (aka “Ultem”) polymer material is UL V-0 rated down to 1.8 mm wall thickness and has a special blend of conductive elements. This material meets the Boeing 7238 smoke density rating of MAX 110 Ds with 3.0 mm @ 4 minutes.
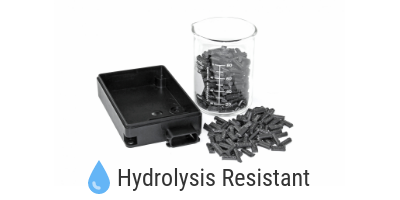
PBT-225
Polybutylene terephthalate
50-75 dB shielding
Hydrolysis resistant
75° C
UL 94 HB
Carbon granules, stainless steel
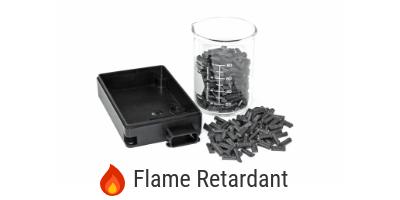
PBT-250-FR
Polybutylene terephthalate
50-75 dB shielding
Flame retardant
75° C
UL 94 5VA
Carbon fiber, stainless steel
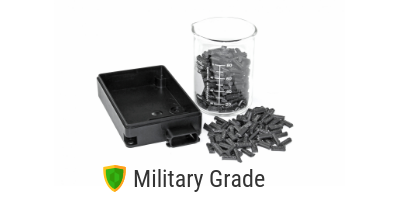
PEI-140
Polyetherimide
50-75 dB shielding
Defense/aero grade
170° C
UL 94 V-0
Carbon fiber, carbon granules, stainless steel
PC-ABS GENERAL PURPOSE GRADES (HT)
Provides up to 85° C continuous use temperature rating and is the most cost-effective grade of our Nickel-Plated carbon fiber and granule filled polymers. A230-HTHF and A240-HTHF versions use “HF” (Hybrid Filler) granular graphite to improve cost and minimize post mold warpage.
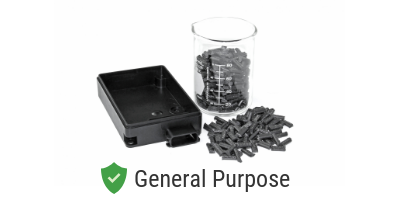
A220-HT
Polycarbonate ABS
40-60 dB shielding
Economical
85° C
Carbon fiber filler
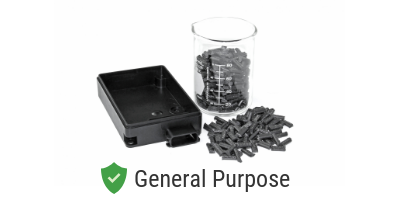
A230-HTHF
Polycarbonate ABS
50-75 dB shielding
Economical
85° C
Carbon fiber/granular filler
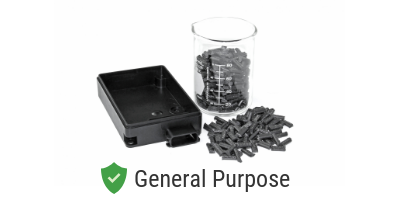
PC-ABS SUPER TOUGH AND ELEVATED TEMPERATURE GRADES (ST)
Provides up to 105° C continuous use temperature rating and the lowest possible surface resistivity for excellent grounding properties. Filled with nickel-plated carbon fiber exclusively to maximize conductive properties of the molded product.
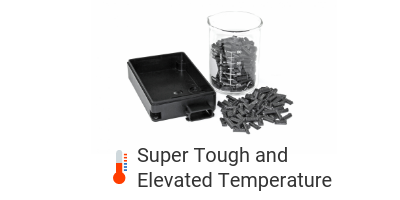
A220-ST
Polycarbonate ABS
40-60 dB shielding
Mechanically strong
105° C
Carbon fiber filler
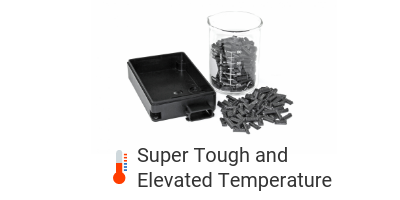
A230-ST
Polycarbonate ABS
50-75 dB shielding
Mechanically strong
105° C
Carbon fiber filler
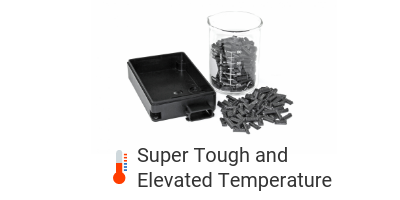
A240-ST
Polycarbonate ABS
75-90 dB shielding
Mechanically strong
105° C
Carbon fiber filler
PC-ABS FLAME RETARDANT GRADES (FR)
UL V-0 rated to 1.5 millimeters wall thickness and provides up to 70° C continuous use. Uses Nickel-Plated carbon fiber and granular fillers. Moderate and high filled versions use “HF” (Hybrid Filler) granular graphite to improve cost and minimize post mold warpage.
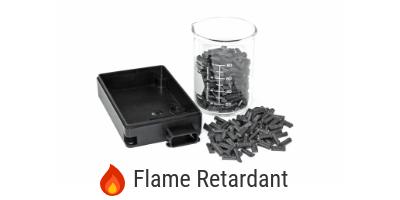
A220-FR
Polycarbonate ABS
40-60 dB shielding
Flame retardant
70° C
UL 94 V-0
Carbon fiber filler
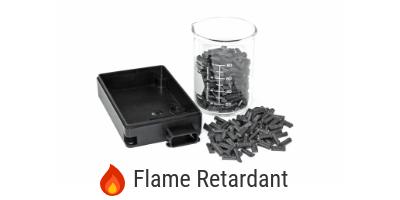
A230-FRHF
Polycarbonate ABS
50-75 dB shielding
Flame retardant
70° C
UL 94 V-0
Carbon fiber and carbon granular fillers
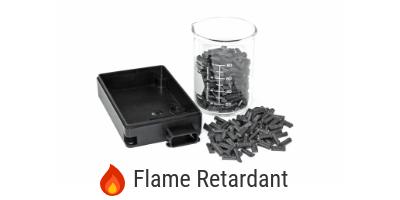
A240-FRHF
Polycarbonate ABS
75-90 dB shielding
Flame retardant
70° C
UL 94 V-0
Carbon fiber and carbon granular fillers
ENGINEERING AND PRODUCT SUPPORT
Our experienced engineers are available to help with optimal material selection and manufacturing strategies for each project. This includes support to ensure properly matched EMI gaskets, product design strategies, tooling, and other needs.
Buy Electrically Conductive Plastic Test Boxes
Test boxes are available as 100mm x 140mm x 85mm in the below materials and give engineers the ability to evaluate our electrically conductive plastic materials in a representative format similar to their end application. All test boxes come with a gasket and are ready for your components.
PREMIER PBT-225
Polybutylene terephthalate
50-75 dB shielding
Hydrolysis resistant
75° C rating
UL 94-HB
PREMIER PEI 140
Polyetherimide
50-75 dB shielding
Military grade
170° C rating
UL 94 V-0
PREMIER 240-ST
Polycarbonate ABS
75-90 dB shielding
Mechanically strong
105° C rating
PREMIER 240-FRHF
Polycarbonate ABS
75-90 dB shielding
Flame retardant
70° C rating
UL 94 V-0
Parker Chomerics can offer advanced engineering support and state-of-the-art manufacturing capabilities to facilitate metal replacement technology in the form of specially formulated polymers for EMI shielding, chemical resistance, excellent thermal properties, and weight/cost savings.
Advanced Engineering Partnership:
• Experts in plastic injection molding technology for thermoplastics that meet design requirements
• Thorough knowledge of FEA technology to plan out physical stress requirements
• Able to facilitate simplification of parts for manufacturing flexibility and cost reduction
• Mold flow analysis for raw material use optimization
State-of-the-Art Manufacturing Capabilities:
• 75,000 square foot purpose-built plastic injection molding facility
• Advanced Certifications (ISO 9001 and 14001, TS16949)
• More than 40 injection molding presses
• Closed loop central material feed system for lean manufacturing
• Cellular manufacturing with automated assembly and testing
• Value added services • ultrasonic welding, hot stamping, testing, press fitting, assembly
• Insert, Two-Shot, and Vertical molding capabilities
• Able to process 300 grades of resin
Typical Markets/Applications:
• Automotive/Transportation (Accumulator pistons, cylinder head covers, lumbar support, vent caps, wiper pivot housings)
• Telecom/IT (Infrastructure, power supply housings, routers, servers)
• Consumer Appliance (Home security, hand tools)
• Industrial/Safety/Electronics
• Military/Aerospace
• Life Science/Medical
Additional Resources