EMI Shielded Air Ventilation Panels
Parker Chomerics EMI shielding air ventilation panels include a range of innovative products and configurations to deliver high performance shielding. Chomerics shielded EMI air ventilation panels combine maximum shielding with minimal air flow resistance to provide optimal airflow for cooling electronic enclosures. These vents can be incorporated into enclosures where EMI radiation and susceptibility is a concern or where heat dissipation is necessary. This ensures long-term assembly performance.
Parker Chomerics STREAMSHIELD™ Vent Panels serve as a high performance, economical solution to EMI and airflow issues for telecommunications and information technology markets. These vents provide a sophisticated solution for regulatory standards to emissions suppression and heat management within electronics housings. There is an incredible amount of customization available, including but not limited to: alternative honeycomb cell sizes and thicknesses, custom sized frames, custom fastener hole patterns, coatings/platings, protective grilles, and specialty hardware.
Why EMI Shielding Vents?
Features and Benefits:
• Lightweight Design
• Economical Solution
• Excellent shielding (50 dB @ 10 GHz)
• Excellent aspect ratio for airflow (95% open area)
• Rapid prototyping and customization
• Availability of intumescent coating for fire containment
Typical Applications:
• Test equipment
• Wireless/Wireline Infrastructures
• Personal Computers
• Network Servers, Cabinets, and Enclosures
• Cellular Base Stations
• Rack-mounted power amplifiers
• High speed routers
Parker Chomerics SHIELD-CELL™ Vent Panels provide maximum EMI shielding with minimum air flow resistance for ventilation within electronics enclosures. These vents are ideal for ready-to-mount applications where an added gasketing (elastomer/neoprene and Monel wire) is able to be compressed along the vent seam for maximum shielding performance.
Features and Benefits:
• Standard size honeycomb contains 1/8 inch cells and 1/2 inch total thickness
• All-aluminum construction
• Chromate conversion coated assemblies
• Ideal for applications that require minimal shielding
• Available with a tin-plating for environmental protection
SLIMVENT™ Space Saving EMI Shielding Air Vents panels are designed for low clearance or critical space limitations and are constructed of expanded aluminum or Monel® (nickel-copper alloy) foil instead of traditional honeycomb.
Parker Chomerics SLIMVENT™ Shielded Vent Panels provide excellent EMI shielding (up to 90 dB) and air ventilation in a specially-designed narrow profile (0.187″” thickness).
Features and Benefits:
• Narrow profile ideal for accommodating critical space limitations
• Panels are made from aluminum or Monel (nickel-copper alloy)
• Added wire mesh gasket for EMI shielding around vent border
• All SLIMVENT™ panels are custom fabricated to specified dimensions
Parker Chomerics SHIELDSCREEN® EMI Shielding Air Filters provide additional protection to EMI vents meant for dust particle collection along electronic enclosure borders
Features and Benefits:
• Filtering provided by layers of woven mesh overlapped onto each other
• Viscous oil coating can be used for additional dust entrapment
• Complete assemblies mean that the vents can be quickly removed and replaced for cleaning
• Dry filters are cleaned by vacuuming from the intake side
EMI Shielding Honeycomb Air Vent Panel Design Features
EMI Shielding Honeycomb Air Vent Panel Design Features – Honeycomb Air Vent Panels – Parker ChomericsHoneycomb air vent panels are used to help cool electronics with airflow and while maintaining electromagnetic interference (EM) shielding. Recently, our team of experts held a webinar on EMI shielding air vent panels, now available on-demand. This blog post will highlight some topics discussed in the webinar.
The most important factors of honeycomb air vent panels are shielding effectiveness and airflow, which are both directly related to the cell size. Both factors have a large impact on the size, material, and design of the vent panel. While you will need to balance the tradeoffs between airflow and EMI shielding needs, you should also ask yourself if air particle filtration is needed as well.
Design features
Durability and the possibility of corrosion in harsh environments have an impact on design. Honeycomb is described in terms of two different size categories: cell size and thickness.
Cell size
Specifies the width of the individual cells. The honeycomb is hexagonal, and the cell size is the measurement across each cell and the thickness is the measurement of the entire sheet of honeycomb material.
Cell size can have an impact on airflow, but it can also have an impact on shielding effectiveness. As a general trend, the smaller the cell size, the lower the airflow or the greater the pressure drop across the air vent panel.
At the same time, the smaller the cell size, the greater the shielding effectiveness because the smaller cell size limits the amount of electromagnetic energy able to pass through the openings. The key is to find the middle ground, the largest opening to allow enough air-flow to cool the system, but also the smallest cell size to block the undesired frequencies and obtain the required shielding.
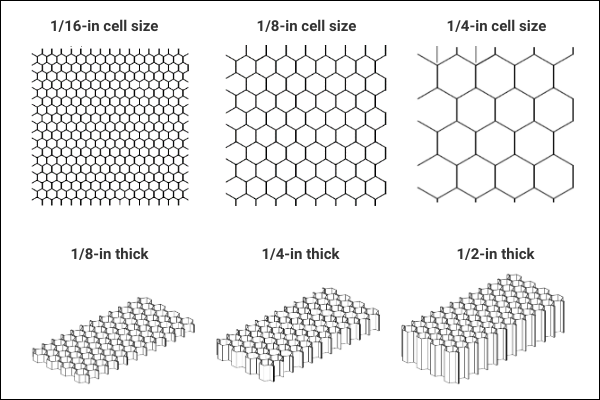
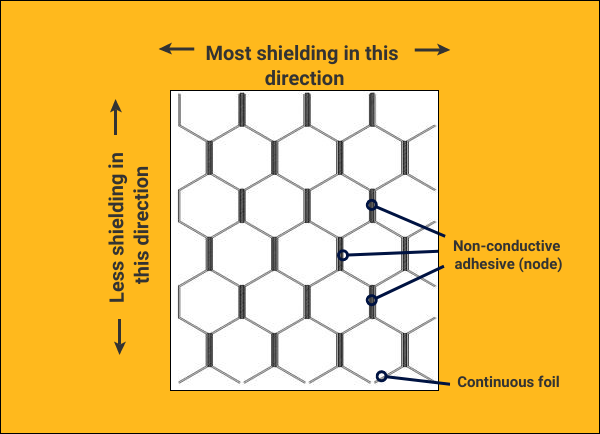
Cell thickness
The thickness of the air vent panel also has an impact on both the airflow and the shielding effectiveness. If the cell size were kept the same, the lower the thickness of the vent panel, the greater the allowable airflow.
The decreased airflow is caused by the surface friction of the air flowing through the honeycomb cells. However, reducing the vent thickness will also reduce the attenuation capabilities of the honeycomb. Again, the key is to try and find the middle ground between good air-flow (less pressure drop) and shielding effectiveness.
Honeycomb construction
Aluminum honeycomb is made from thin ribbons of bent aluminum that are adhered together using a non-conductive adhesive. The points at which the ribbons come together are known as nodes and can cause EMI shielding leakage. With single-layer honeycomb vents, there is actual directional EMI shielding. This is known as the polarization principle.
It’s also important to note that this is only the case with aluminum honeycomb vents because, with brass and steel vent construction, the nodes are welded together and therefore are inherently conductive.
OMNI-CELL™
One way to reduce the directionality of attenuation in vent panels is by using what Parker Chomerics calls an OMNI CELL construction. This means that the second layer of aluminum honeycomb is stacked on top of the first at a 90-degree angle.
The directionality is offset by the second layer and the new panel should have nearly equal attenuation in both directions. One small drawback is that the two layers will reduce airflow across the new vent panel.
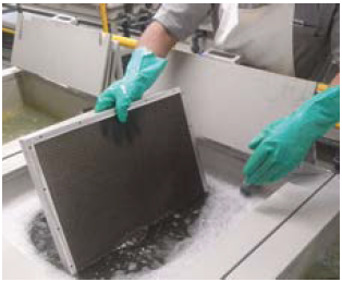
Platings and coatings
OMNl-CELL can be a great option in many cases, but for applications where an OMNI-CELL construction will not work because of space or high attenuation needs, you can achieve the same effect by plating the honeycomb. The plating of aluminum honeycomb will bridge the non-conductive node, and eliminate the directional effect of the honeycomb.
It’s also a much more thorough coverage, which results in better shielding. Platings will protect the vents from corrosion and standard wear and tear. Electroless nickel is one of the most common plating options, as is a chromate conversion coating.
And lastly, EMI vents can be coated with aesthetic paints to match any enclosure design. This includes CARC paints and common military color patterns.
Parker Chomerics can offer advanced engineering support and state-of-the-art manufacturing capabilities to facilitate metal replacement technology in the form of specially formulated polymers for EMI shielding, chemical resistance, excellent thermal properties, and weight/cost savings.
This blog was contributed by Jarrod Cohen, marketing communications manager, Parker Chomerics.