Four Critical Design Considerations for Quality Form-in-Place Gaskets
When it comes to packaging for your electronics, electrical isolation and complex cross-section patterns are often required. The solution? Form-in-Place (FIP) gaskets.
Form-in-Place (FIP) gaskets are hugely important in the manufacturing industry, recognized widely as a cost-effective, functional seal for dense electronics packaging. FIP can replace wire mesh gaskets, molded-in-place or die-cut gaskets. Characteristics of these gaskets include:
- Assembly not necessary.
- Optimal flexibility, sealing any and all gaps.
- Compartmentalized shielding.
- Minimal scrap material.
- Excellent positioning tolerances.
- Rapid gasket size and location changes as needed without tooling
The design of the gasket is essential to keeping what you want to have in, and what you don’t want out. For tips on how to prevent quality issues, reducing cost, and, of course, delivering a quality product on time, read on!
1. Design for RF Field
When sealing two or more mating pieces, it’s important that grooves are factored into your product design. These grooves allow for a proper gasket seat designed for an O-ring. In the absence of grooves, the O-ring would become distorted.
It takes several factors to craft the perfect groove and basket pairing. For optimal performance, it’s important to consider the following:
- internal diameter
- internal perimeter
- cross sectional diameter
- O-ring or gasket stretch percentage
- percentage squeeze
- O-Ring or gasket volume (and more.)
Of course, when the design is finalized, these factors need to be tested for performance and functionality.
Form-In-Place gaskets
When seal design is complicated, Form-in-Place gaskets are an especially helpful solution. This application requires extremely precise placement.
The adhesive capability of this application allows for a groove design to not be included. In fact, sealing can effectively be applied in small areas without grooves when using a form-in-place gasket. When executed properly, each of these factors will positively influence your cost-savings.
2. Materials
Thanks to modern technology, the material options for form-in-place gaskets can be matched to your application requirements. Features like top-of-the-line shielding, adhesion, heat and humidity resistance, and reliability low compression sets make the form-in place gasket. An excellent choice to meet your EMI Shielding requirements.
Worried about conductivity?
Conductive and Non-Conductive Silicone and Fluorosilicone compounds have excellent environmental stability to heat, cold, moisture, UV, ozone, galvanic corrosion or pressure. When combined with an electrically conductive filler like silver, copper, nickel, aluminum, ferrite or graphite particles, silicone-based elastomers make excellent shields for EMI/RFI shielding.
Nickel vs Graphite Conductive Silicones
For example, the low-cost Ni/Graphite filler makes 5560 a >65 dB shielding material while also providing a good galvanic corrosion-resistant gasket when mated with aluminum for outdoor applications.
Nickel graphite EMI Shielding is trusted by groups like the US Military, speaking to the quality and functionality of the product and ensuring that it will suffice for your design. Nickel graphite has high-performance shielding, salt spray and corrosion qualities, and is now making its way into commercial applications. Some of these applications include medical, automotive and wireless technology. If you’re looking for EMI shielding for any of these applications, be sure to consider these characteristics for optimal performance.
3. Tolerances
Tolerances are essential to optimal design, with height being the most crucial physical tolerance specification for form-in-place gaskets. The height of the tolerance determines what the width of that gasket will be. The height can change, as it is dependent on the dimensions of the part and different varieties of dispensing parameters. On the other hand, the width of the gasket is dependent on height. This is due to the free-forming process and the viscosity of the material. All things considered, both height and width must be considered in your design.
Here are the recommended specifications and tolerances for your dispensed gasket design:
- Height within tolerance (< 0.04in +- 0.004in, 0.04-0.06in +- 0.006in, >0.05in +0.01in -0.0.06in)
- Adhesion of the gasket (normally 0.024 N/in² in shear force)
- Resistance (stable resistance is a good indicator of stable process)
- Surface of Ni/Sn should have max resistance of 50 mohm
- Surface of Al or passivated Al should have 200-600 mohm
- Adhesion of the gasket is typically specified as a minimum of 0.024 N/in² in shear force.
- Specifying resistance maximums is another step to ensure the quality of the production process.
- The electrical resistance that can be measured on the conductive gasket depends on the surface conductivity of the part.
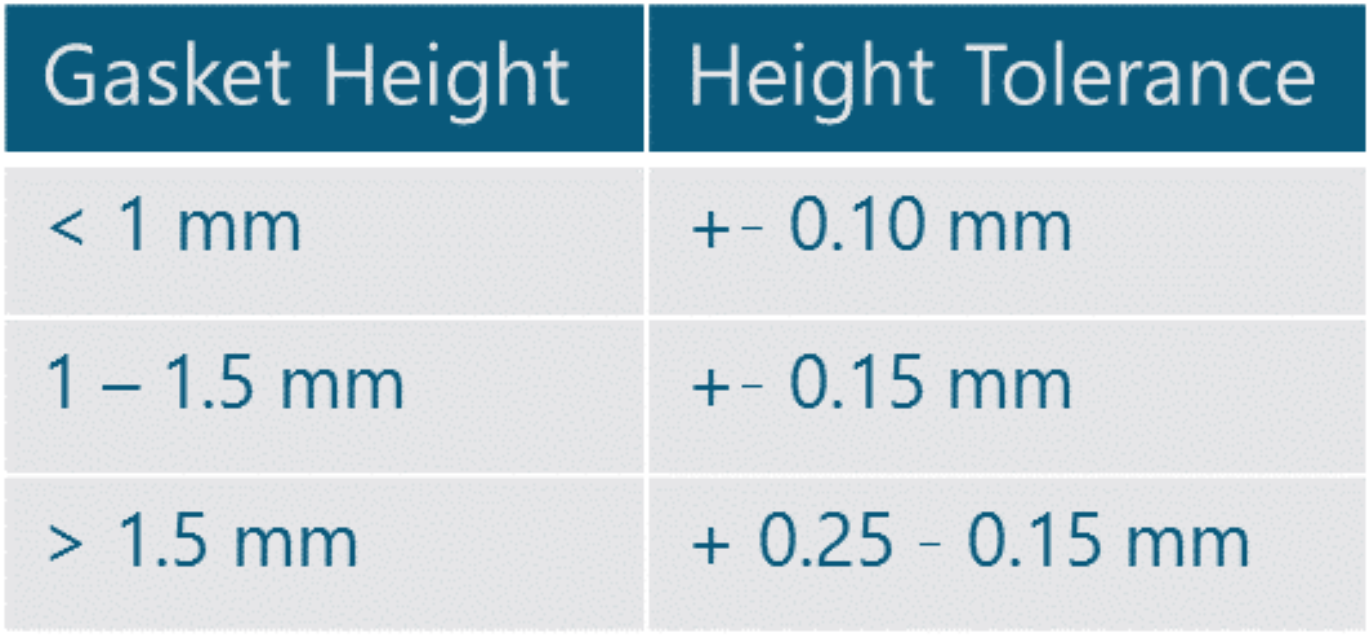
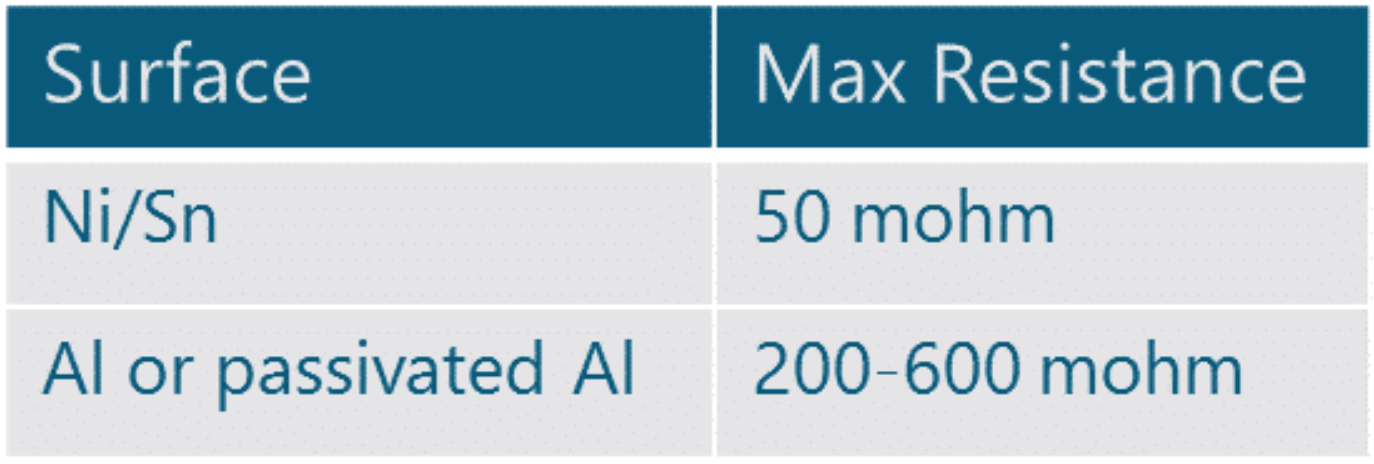
4. Supply Chain
One of the greatest benefits gained from using form-in-place gaskets is that the supply chain process is shortened. This warrants a more efficient, streamlined production process and overall cost savings. When opting for a custom manufacturer like KRA Fabrication, you can order and receive your parts with no gasket inventory to maintain, no assembly required, and no reshipment needed.
Here’s how it works:
- Send design to the manufacturer.
- Your Custom Manufacturer will precisely mill your parts or have them milled by your preferred machine shop.
- The manufacturer will apply form-in-place gasket material to your design.
- Your parts will then be shipped, ensuring timeliness and quality assurance by your custom manufacturer.
That’s it!
Is your process this easy?
Ask yourself the following questions if you’re not sure how or where to start improving your process:
- How many times are parts shipped back and forth between manufacturers before design is complete?
- What is the repackaging and labor cost in shipping those parts?
- Does too much handling cause Quality Control issues?
- How much staff is required to manage the supply chain?
The most efficient, cost-effective and timely solutions are found through custom manufacturing. Ensure your gasket arrives on-time and within budget. Contact us here to learn how.