Thermal Gap Pads vs Thermal Conductive Paste
Thermal interface materials ensure air gaps between electronic components are completely eliminated which is required to keep device temperatures at a safe operating level. Engineers often consider the specifications around a heat sink to find a solution that’s suitable for their application.
How Do Thermal Interface Materials Work?
TIMs are often placed between two or more heat-sensitive manufacturing components. Afterall, a typical contact area can have up to 90 percent air voids. Thermally conductive materials transfer heat to the surrounding environment, ultimately protecting components from heat-related adverse reactions.
These materials need to have two key properties, which are thermal impedance and thermal conductivity. Thermal impedance measures the efficiency of heat being transferred to the surrounding areas. Thermal conductivity is the natural ability of a material to transfer heat.
Deciding Between Thermal Gap Pads and Thermal Paste
It’s important to understand which type of thermal interface material, such as gap fillers, an application needs.
Fillers are used in widely different cases based on the nature by which they must be applied. It requires very specific placement and pressure during installation.
But which filler – thermal gap pads or thermally conductive paste – is right for your application?
Thermal Gap Pads
Thermal gap pads are soft, conformable pads that help reduce component stress and dampen vibration, in addition to their thermal properties. Its thermal conductivity generally ranges from between 1 to 6.5 W/mK, and though the standard thickness usually falls between 0.010” to .200”, it can also be thicker. Your material choice for thermal pads will depend on the needs of your design. For example, fiberglass and aluminum carriers are both popular choices. Meanwhile, shear-resistant Kapton and PEN film are used in applications where shearing is a risk.
Advantages of pads
Thermal pads are easy to apply and do not require the same kind of specialized application equipment as paste. Simply put, the pads need to be laid onto their application with relative pressure.
Thermal pads are sometimes included with the heat-producing component to bypass the pad adhesion, making the manufacturer’s job even easier. Similarly, thermal pads are far less likely to shift out of their initial position compared to thermal paste.
They have a standardized heat dissipation capacity across the surface of the pad compared to the thermal paste’s liquid state, making that standardization more challenging to achieve. Upon application, the pad will react to the heat-producing component’s temperature by softening and therefore enabling the pad to fill interfacial gaps in the surface of the application.
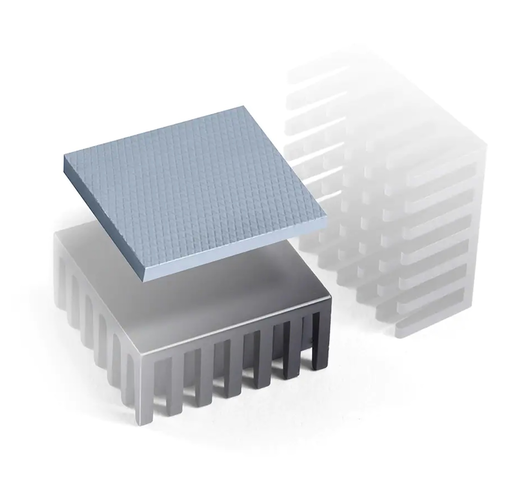
Disadvantages of pads
As there are two sides of every coin, thermal pads also come with their own disadvantages depending on the application at hand.
As thermal pads adhere to the heatsink, the pad will oftentimes mold to one of the heat-producing surfaces it touches. So, thermal pads must be replaced if the heatsink or other components nearby are moved.
Thermal pads cannot be used more than once, and if removed, each component must be handled with extreme caution – especially once the pad has adhered to other components of the application.
Thermal Conductive Paste
Advantages of thermal paste
Thermal paste offers a similar solution to thermal pads, but being a liquid, the paste can be used in several ways that a thermal pad cannot. The paste is applied via dispenser (syringe, tube, etc.) directly to the central processing unit (CPU) or the heatsink, filling even the smallest interfacial air gaps to ensure efficient thermal transfer and conservation.
Pastes were first developed for use in automotive manufacturing. That means they were designed to not flow and be stable through intense vibrations, as well as holding up over time.
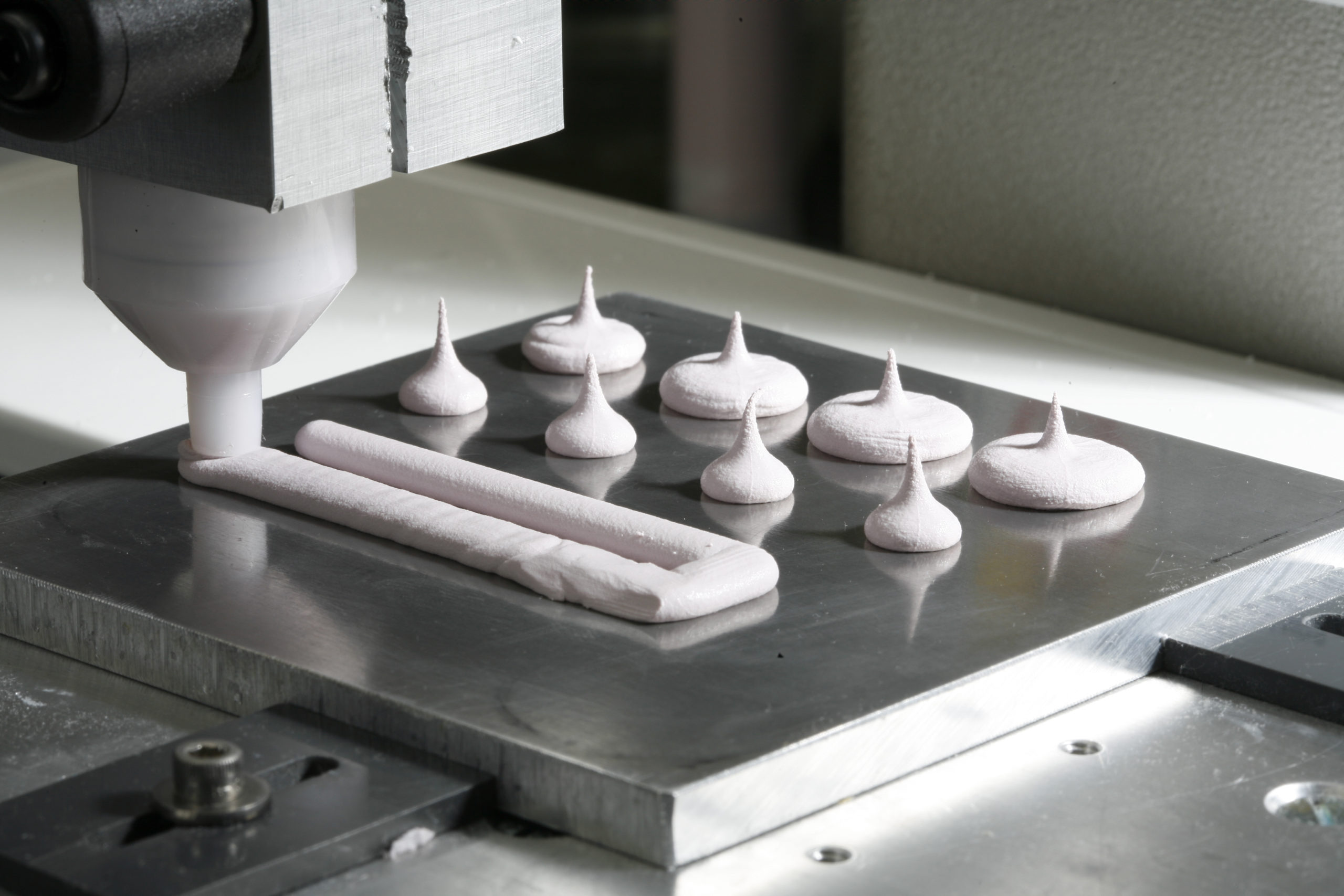
Another key benefit of using thermal paste is the efficiency of the material. Very little paste is needed, as the heat transfer capacity is inversely correlated with the amount of thermal interface material used. For example, the THERM-A-GAP GEL30 or GEL8010 has low thermal impedance at thin and thick gaps, allowing the use of common heat spreaders.
In other words, the TIM is most effective when a very thin layer is used, as opposed to using a more generous amount of the material. Of course, it’s important that enough of the material is used to fill all necessary gaps.
Choosing a thermal conductive paste that passes NASA outgassing standards is crucial whenever the product is being applied near camera or optical components. Low outgassing ensures that outgassed silicone won’t condense onto cameras or other optical equipment.
Disadvantages of thermal paste
While thermal paste certainly has several desirable properties – especially compared to their pad counterparts – it’s important to understand the potential risks associated with a material that requires manual application techniques.
When applying, it’s crucial to ensure that the entire surface area is covered as needed, and enough is used. While less is typically more when it comes to thermal paste, using too little will not adequately fill any air gaps that may be present.
The liquid state of thermal paste can lead to a mess and wasted material, so caution and precision are key.
Which is better: Gap Pads or Conductive Paste?
The answer? It depends.
Your performance demands and design needs will determine what’s best for your product.
Can I use thermal paste instead of thermal pads?
Thermal paste, or gel, can be a smart alternative to thermal pads. Thermal paste offers some advantages over thermal pads; such as automation capacity, lower impedance (in certain material scenarios), and they can have higher conformity to irregular surfaces.
You may want to consider thermal paste if:
- Your production needs are upwards of 5,000 units/year.
- The design of your parts involve complex or intricate patterns.
- Your parts are delicate, as the mechanical stress from paste is low.
If you plan to replace thermal pads with thermal paste, you may look at Chomerics Therm-a-Gap Gel 75 as it has a high thermal conductivity. Or consider Gel 30 or 8010, which have been used in automotive applications and have ultra-low compressibility.
Are thermal pads better than thermal paste?
This is a common question due to the historic and wide-spread use of thermal pads. It’s true that there may be difficulty laying a perfectly consistent amount of paste across a given surface. However, paste is typically applied automatically, whereas pads have been applied manually to-date.
Vibration and space-filling are two characteristics which are typically best fitted to the qualities of thermal pads. Thermal pads can dampen vibration and decrease the long-term disruption applied by vibratory stress.
If there are large gaps, especially near heat sinks, a thermal pad could be better than a paste. In that case, an exorbitant amount of paste would be required, potentially exceeding cost-efficacy and long-term predictability of performance.
While there are some applications in which thermal pads are better than paste, it truly comes down to the purpose of your part.