Successful Form-in-Place Gaskets
Form-in-Place (FIP) gaskets are a cost-effective choice as a sealant for close-packed electronics. When isolation and cross-section patterns are required, FIP gaskets are the best-in-class value.
To ensure that zero-leak requirements are met, it is essential that the joint be designed with gasket-specific guidelines.
Benefits of Form-in-Place gaskets
- No assembly is needed
- Superior flexibility to close any gap
- Compartmentalized shielding
- Little scrap material
- Excellent positioning tolerances
- Replaces wire mesh, molded-in-place or die-cut gaskets
In order to achieve the highest quality, the most cost-effective product on time, form-in-place gasket production requires excellence from design to delivery. This excellence depends on no groove, great material, high tolerance, and a short supply chain. Learn more tips for successful form-in-place design.
No Groove
Grooves are common in the design of parts and are often required for reliable sealing of two pieces. They provide a solid gasket seat and are necessary for O-rings, which are highly susceptible to distortion. The complication of designing the groove/gasket combination lies in very specific and correct calculations.
With form-in-place gaskets, a groove is not necessary. This eliminates the need for intricate seal design and the applying of a seal into a groove, both of which require time and cost.
The flexibility of form-in-place, with its adhesive capability, eliminates the need for a groove in your design. The dispenser accurately lays down a bead where you want it with your chosen material and requirements.
Form-in-place gaskets allow you to design the most intricate part, with multiple compartments, in small and tightly compressed areas, with no grooves needed for reliable sealing. This means major savings in both time and money, which is KraFAB’s goal for any customer.
Materials
Due to the advancement in technology, there is now a vast range of materials available for FIP gaskets. Excellent shielding effectiveness, superior adhesion, heat and humidity resistance, and reliability in low compression are all available for form-in-place gasket material options.
Cost is the most important factor when deciding on nickel graphite versus silver for EMI/RFI shielding. With the increase in silver cost, it is too expensive to be the material choice any longer. EMI/RFI shielding elastomers are the perfect alternative since they do not sacrifice shielding, corrosion resistance, or physical properties.
The U.S. Military uses these elastomers since they meet their stringent requirements, making them a cost-efficient solution for any design. The high-performance shielding qualities of nickel graphite are used in commercial applications such as medical, automotive, and wireless technologies and will be ideal as your material selection, as well.
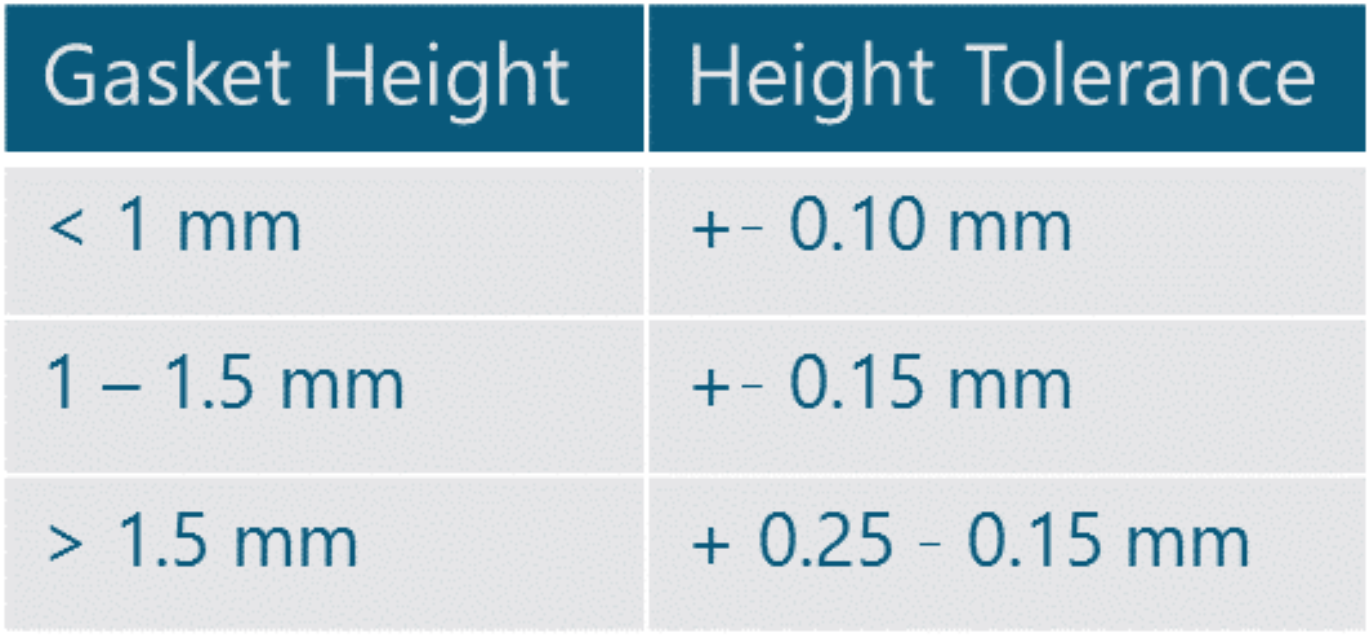
Tolerances
In addition to the right material, proper tolerance is critical to product design. With form-in-place gaskets, height is the most important physical tolerance specification. Height also determines gasket width, since it depends on the variation in the dimensions of the part and the dispensing parameters.
The width is also dependant on the height due to the free forming process and the viscosity of the material. These factors make both width and height critical considerations in design.
Supply Chain
Once the design has been chosen from best-fit materials and tolerances, a short supply chain will ensure cost-efficiency. A great customer manufacturer should be able to take your submitted design, get the product to you on-time, and the part should arrive ready to go.
Steps to a Short Supply Chain for Form-in-Place Gaskets:
- Submit your design
- Manufacturer precisely mills the parts
- Form-in-place gasket material applied meticulously
- Parts shipped on time
If these steps are NOT your current process for ordering and receiving your parts, consider the costs:
- How many times must your part be shipped to different locations?
- How much are you losing in re-packaging and labor costs?
- Are parts damaged by so much handling?
- How much is spent on tracking your parts?